
102 Dwellings by Dosmasuno Arquitectos
Spanish architects Dosmasuno have completed an apartment block in the Madrid suburb of Carabanchel.
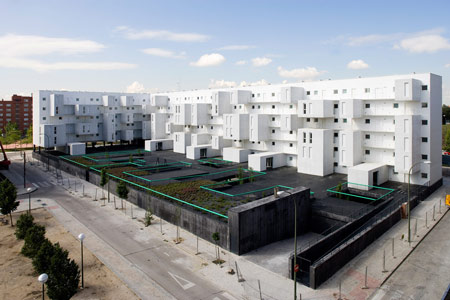
The block consists of 102 apartments of the same layout, with further bedrooms housed in protruding modules.
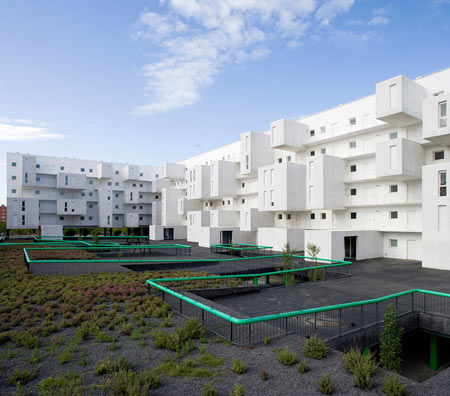
The apartments' living areas are protected from the sun's radiation by a galvanised white mesh.
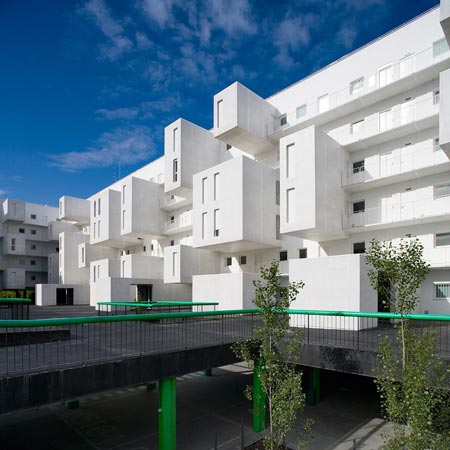
All photos are copywrite of Miguel de Guzmán.
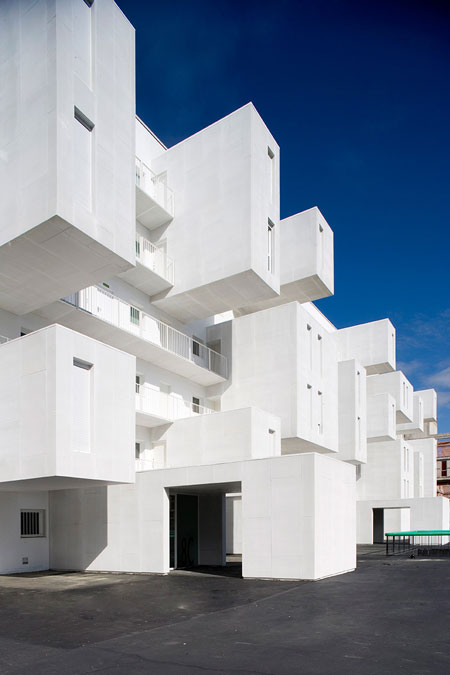
The following is from Dosmasuno:
--
FOOTPRINT
Orientation and introspectiveness
Despite the guidelines drawn on the plots, places need to express their own personality, to arise naturally, to construct themselves.
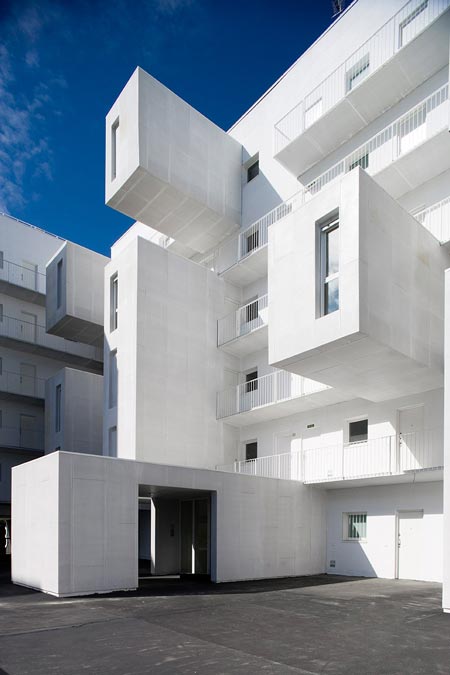
And concretely this one is aligned against a green area, against the concatenation of public spaces that link the old Carabanchel district with its forest through the new neighbourhood.
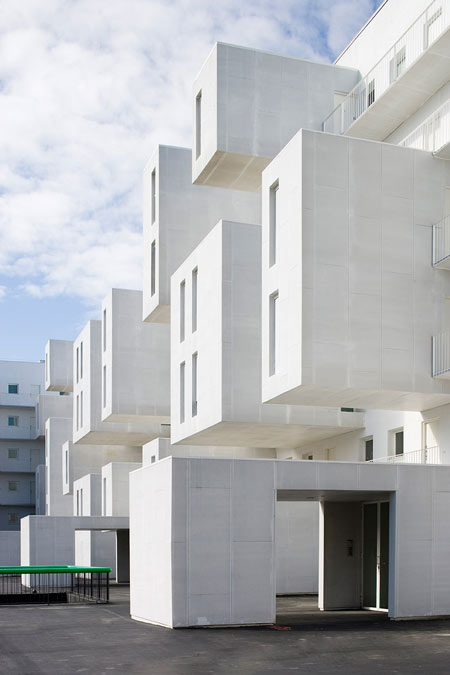
In response to these conditions, the dwellings are compressed onto one edge, onto a single linear piece, in search for the genus loci of the place, views and an optimal orientation in which east and west share the south, generating the limit of the activity, soothing the interior and defining the exterior.
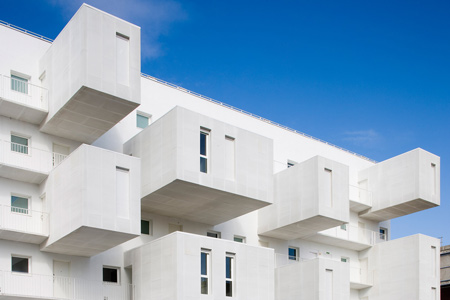
STRATEGIES
Minimum core + additions
The dwellings are designed from an invariable core with a modulated addition which completes the requirements of the program.
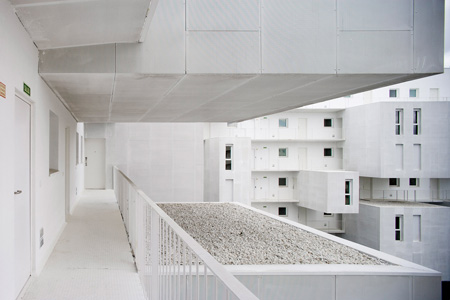
This fixed core is constructed attending to the surrounding views and sunlight, and its two main pieces, living and sleeping rooms, are stacked to the south limit, from which they are protected with a filter, relegating a services strip to the back side.
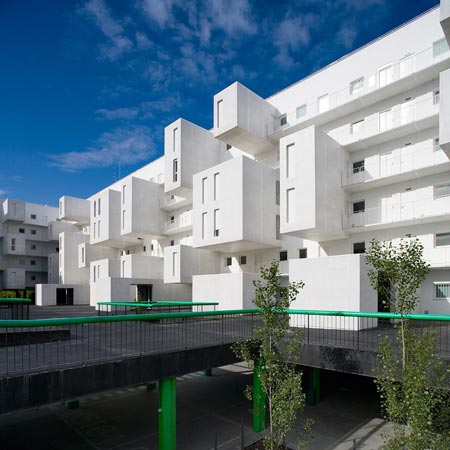
Behind this strip, and like clouds drifting over the void, variations are introduced by the addition of programmatic pieces that form the dwellings of two and three bedrooms.
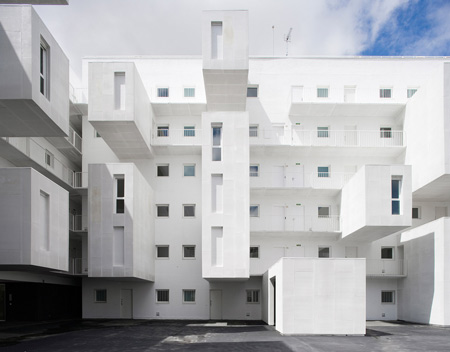
The strict order achieved by the linear core is mathematically blurred into a shifting volume. Thus, the dwellings become “machines for living”, and they are designed as such, fitting surfaces and diminishing the transition areas of between rooms.
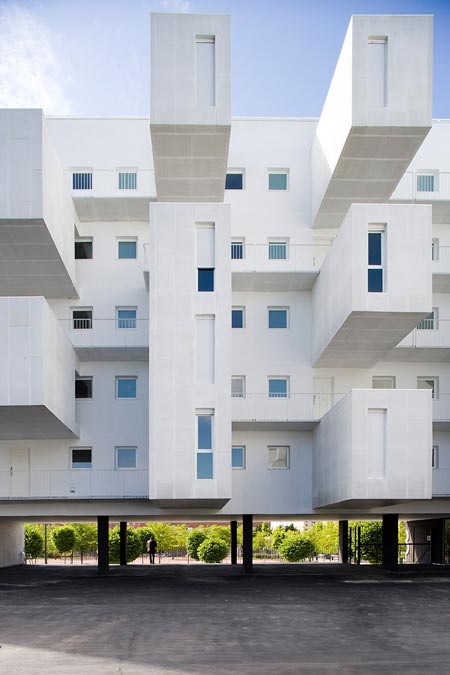
BUILT
Modular casting system
Its construction responds to a necessity of industrial optimization. Therefore, the structure of the main body is constructed in concrete from a single high accuracy aluminium cast.
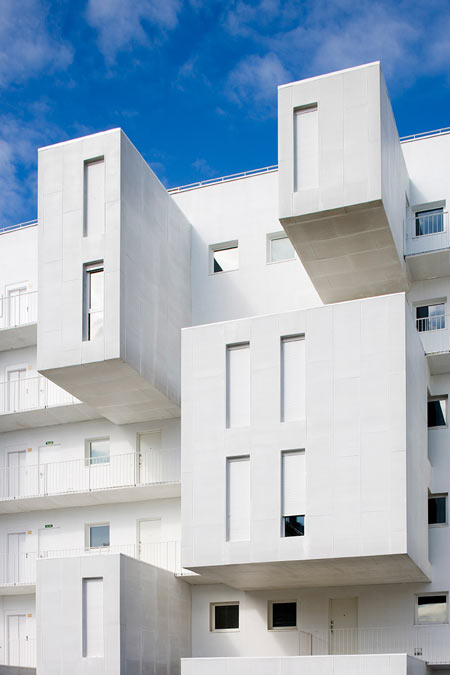
At the same time, the light steel structure modules that constitute the additioned elements enable volumetric variations. This industrialized system facilitates the constructive process, avoiding rubbish and accelerating the implementation times.
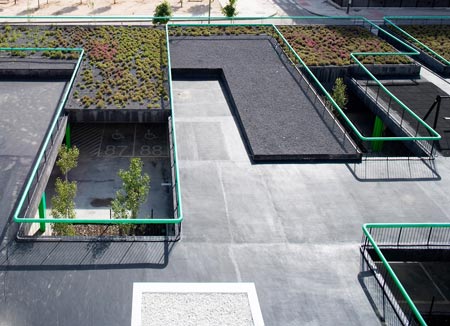
(The following lines feature a more technical approach to the building process)
High accuracy casts have already been used by the EMVS, who had the chance to test their results and performance. This project introduces an important innovation in the constructive process by fabricating the casts in aluminium.
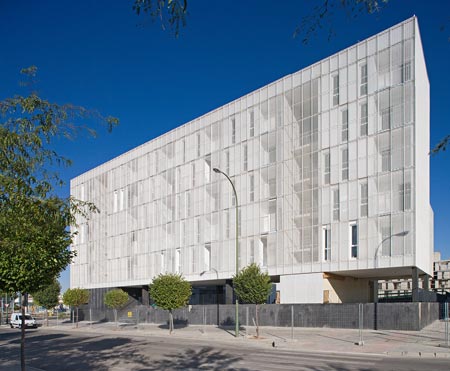
This implies a considerable lightening of the pieces, which enables the workers to manipulate them safely and without any additional cranes.
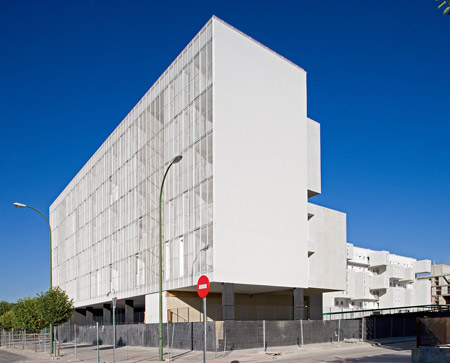
The Project for 102 social dwellings in Carabanchel consists of 52 single-bedroom dwellings, 35 double-bedroom dwellings and 15 triple-bedroom dwellings.
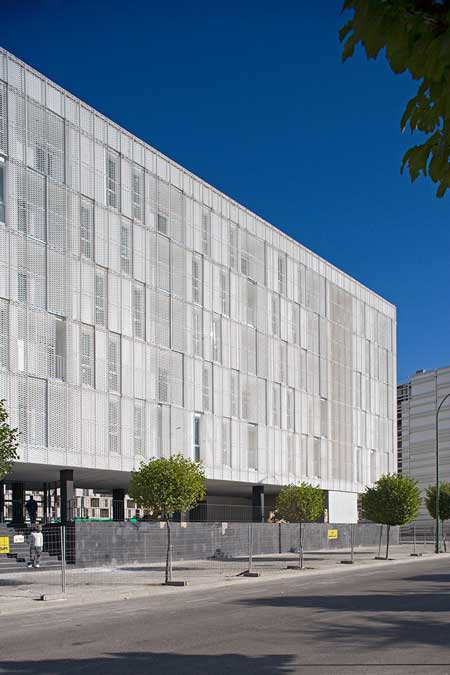
A common dwelling cell was developed for the single-bedroom typology, which becomes double or triple-bedroom typology by the attachment of cantilevered additions.
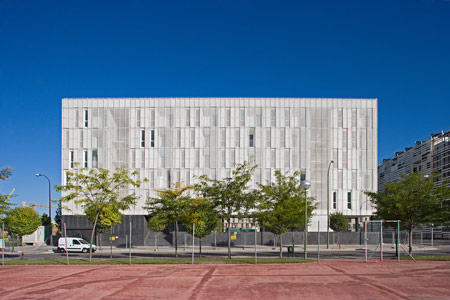
Thus, the project is made up of an invariant core- repeated 102 times- which justifies the implementation of this industrialized system.
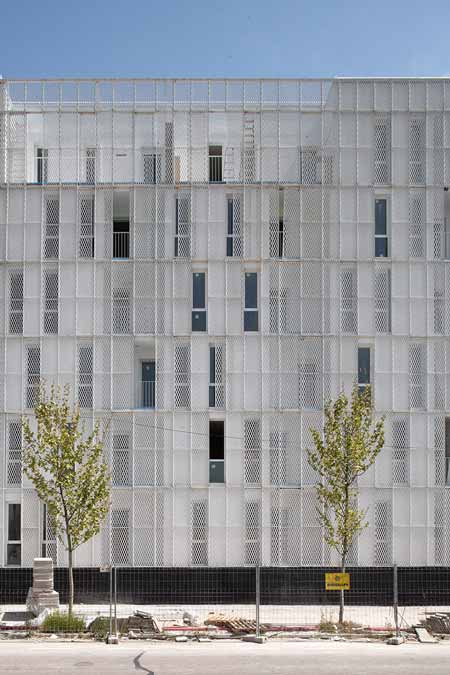
The aluminium casting system defines the core’s distribution (single-bedroom dwelling), including façades, dividing walls, partitions and even wardrobes. These walls contain, once cast, an isolating sheet (the external ones) and the whole services network.
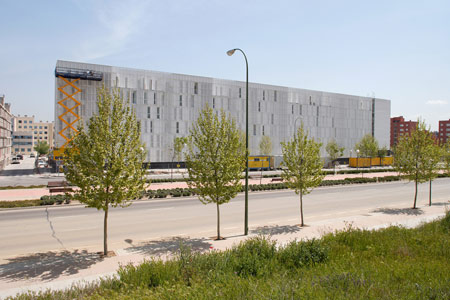
Extra-bedrooms, added in order to extend the dwelling surface, consist on light steel structure modules which are attached to the concrete façade, and fixed to pre-set hangers.
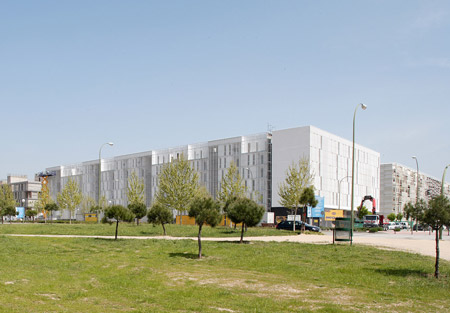
Once again, this system responds to the necessity of an optimized industrial process: a main concrete body, accurately cast with the single aluminium ‘mould’ plus the light skeleton additions, which enable the façade variations.
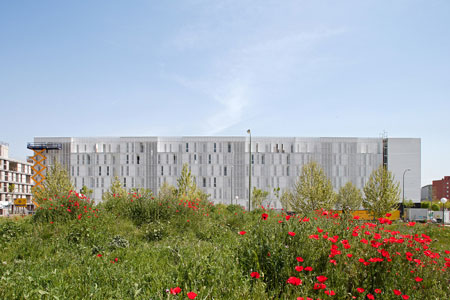
The process is similar to the one implemented in the industrial automobile production system, in which each worker is committed to a single assembling phase, increasing the efficiency of the whole chain.
It starts with the layout of the dwelling walls on top of the lower slab, and continues with the setting of the vertical reinforcements, which are able to stand by themselves.
Then, spacers are put in order to keep them in a straight position, as well as the isolating panels (just in the façade walls), located between the vertical reinforcements.
The walls’ girth has been simplified into two types: façade walls, 24 cm (10 cm + 4 cm insulation + 10 cm) and the rest -dividing walls, partitions and wardrobe walls-, 10 cm. They are all bearing walls. Once the reinforcements and the isolation panels are set, the services are placed into the 10 cm-girth walls, with the exception of the heating system, which is distributed throughout the slab’s girth perimeter.
The next step is the setting of the aluminium cast, coming entirely from the nearby dwelling, and the concrete pouring. Last but not least, window placing, paint job, floating parquet setting over the auto-levelling slab and bathroom and kitchen tiling.
The execution rate is daily, for it is possible to set/remove the casts and pour the concrete within the same day, being able to work on other tasks at the same time. Henceforward, the system performance is one dwelling per day. The advantages of this industrialized system are the quick setting-up, which speeds up the execution period and avoids rubbish production.
On the other hand, it implies an increase in the material cost, due to the amount of concrete used, greater than in conventional construction. The system implies a possible disadvantage concerning the user, and this is the scarce possibility of carrying out further renewals within the dwellings, for every single wall has a structural role.
However, this possibility was dismissed for two reasons: firstly, as the dwelling surface is rather limited (between 42 and 66 sqm), other spatial possibilities would be quite similar to the established, and secondly, and most important, the dwellings are intended to be hired, and, therefore, any extension/renewal would be forbidden.
The external finish ensues as a result of the building’s different orientations, in order to achieve an adequate climatic response, as well as a sustainable climatic performance. The main rooms (living room and main bedroom) of each dwelling face South-East/South-West, whereas kitchens, bathrooms and secondary bedrooms face North-East/North-West.
The insulation mass is mainly kept in the internal part of the façade, increasing the dwelling’s thermal inertia. In winter, this prevents the building from a quick loss of its temperature, whereas, in summer, it helps to avoid extra heat from the outside.
In addition to this main insulation system, a white galvanized deployé façade is placed in the southern façades (white is the most reflecting colour and, therefore, the least solar-radiation absorbing), creating a ventilated double skin, set horizontally in the South-East side and vertically in the South-Western.
This allows the winter’s horizontal solar radiation inside the skin, avoiding the summer vertical one, and concealing the building from the strong western exposure in Madrid’s summertime.
The northern façades are painted white, and the cantilevered bedrooms are covered with drilled, galvanized metal sheets, white as well, working, once again, as a ventilated façade and protecting the inner sprayed polyurethane foam insulation.
Services are centralized and distributed to each dwelling through the access terraces’ structure, and thus avoiding any possible interference with the main concrete body. There is a solar-energy supporting system in the rooftop, also centralized, as well as a pre-installation for an air conditioning system in each dwelling, hidden from the external views.
The service centralization is organized in the basement floor, open to the outside by means of huge voids, through which trees will emerge, and around which cars will be parked.
Architects: Ignacio Borrego, Néstor Montenegro and Lina Toro (dosmasuno arquitectos)
Developer: EMVS. Empresa Municipal de la Vivienda y Suelo de Madrid
Construction company: Begar
Quantity surveyor: J. Mach and J. González
Structural advisor: José Luis de Míguel
Consulting engineers: GRUPO JG
Photographer: Miguel de Guzmán + dosmasuno
Construction beginning: September 2004
Construction ending: November 2007