"4D-printed" shape-changing dress and jewellery by Nervous System
Massachusetts design studio Nervous System has developed a method of 3D-printing jewellery and garments with articulated joints so they automatically change shape once removed from the printer (+ movie).
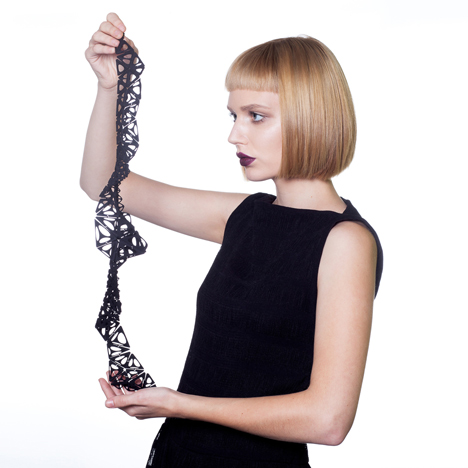
Jessica Rosenkrantz and Jesse Louis-Rosenberg of Nervous System describe their Kinematics project as an example of 4D printing, an emerging area of research which involves printing three-dimensional objects that automatically transform from one shape to another.
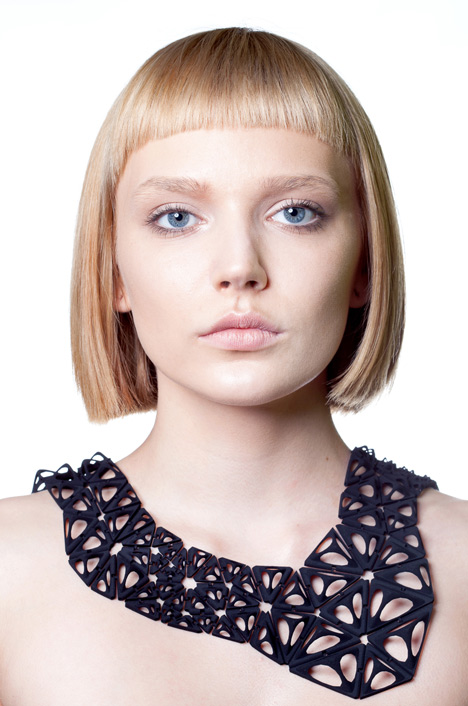
Although it's long been possible to create larger structures by 3D-printing them in sections then manually assembling the components, what sets 4D printing apart is that the finished object will self-assemble or transform into a pre-determined form.
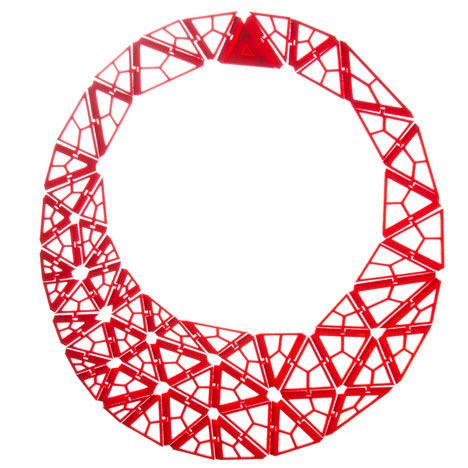
"4D printing refers to 3D-printing something in one shape that is intended to be in another shape," creative director Jessica Rosenkrantz told Dezeen. "The design transforms into its final configuration without manual labour. The shape it is printed in may be advantageous for various reasons: faster, cheaper, or printing larger objects in a smaller volume."

Nervous System are currently working on a dress that can be printed in one piece despite being much larger than the space inside the printer and have also developed a range of jewellery with articulated joints that automatically adapt to the form of the body despite being printed in flat sheets.
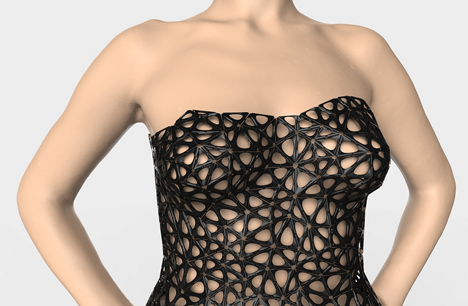
The designers first developed software to give any 3D model a flexible structure, made from tessellated triangles linked by built-in hinges. A second process then folds the model automatically to compress it into the smallest possible volume, optimising the use of space inside a 3D printer. The object simply unfurls into its intended shape once lifted out of the printer.
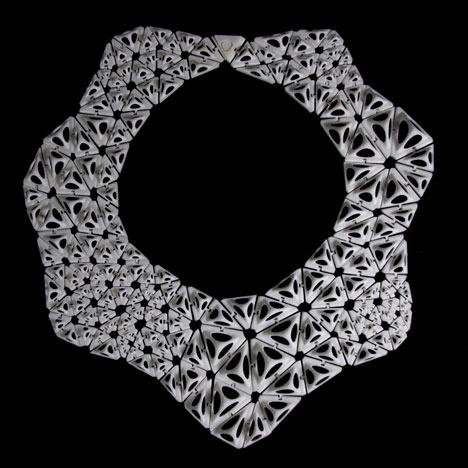
They named the process Kinematics after the branch of mechanics of the same name - also referred to as the geometry of motion - that describes the movement of objects but not its cause.
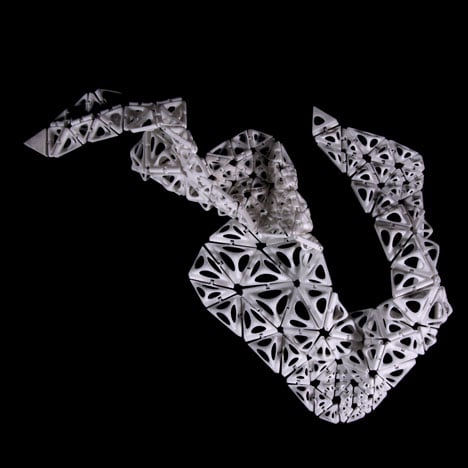
"We think the greatest advantage of Kinematics is that it can transform any three-dimensional shape into a flexible structure for 3D printing," Rosenkrantz said. "The system then compresses the structure down through computational folding."
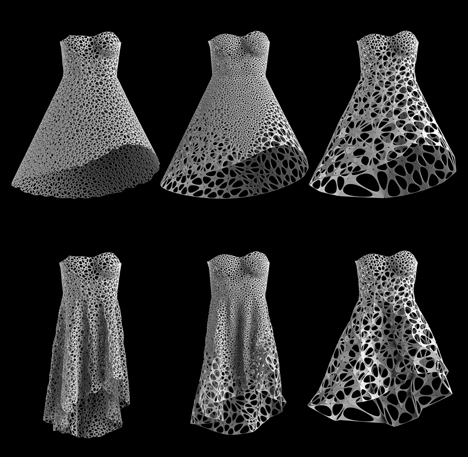
To create the dress, a 3D-scan of a person's body forms the basis for a digitally modelled garment, to which the tessellated pattern is applied. The rigidity and behaviour of the final dress can be controlled at this stage by altering the configuration of the triangular hinged mesh: the way the material will drape as a result is simulated on-screen. This digital model can then be folded into a much smaller shape using computer simulation software and printed in compressed form. When the dress is lifted out of the printer, it will unfurl into its intended shape.
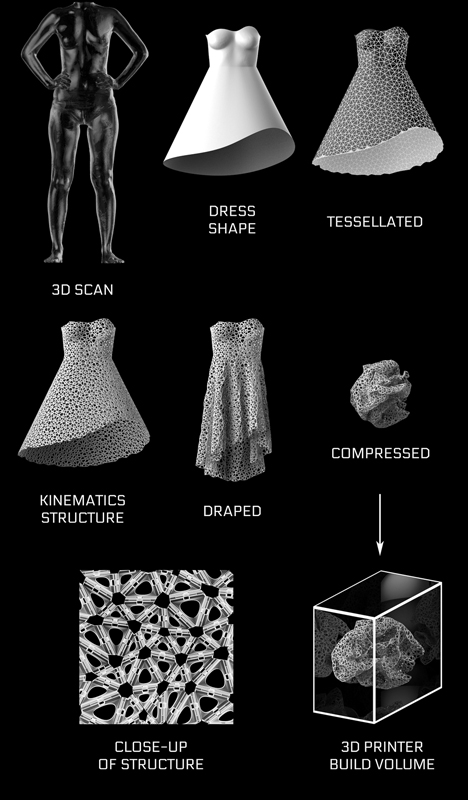
"Compressed designs offer benefits not only for production but also for transport," Rosenkrantz added. "It holds great promise for the creation of flexible wearables but could also be used to enable the production of other large-scale structures in today's small-scale printers."
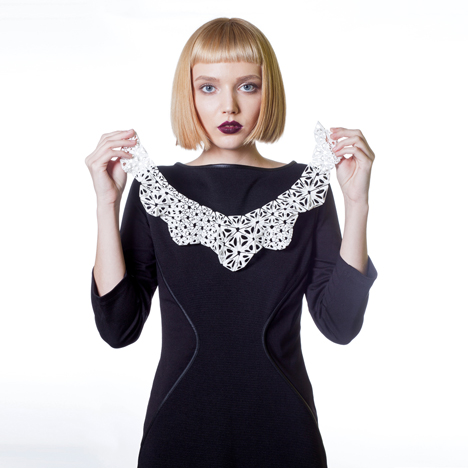
Nervous System began developing the Kinematics concept last year in response to a brief set by mobile phone manufacturer Motorola to create customisable 3D-printed products.
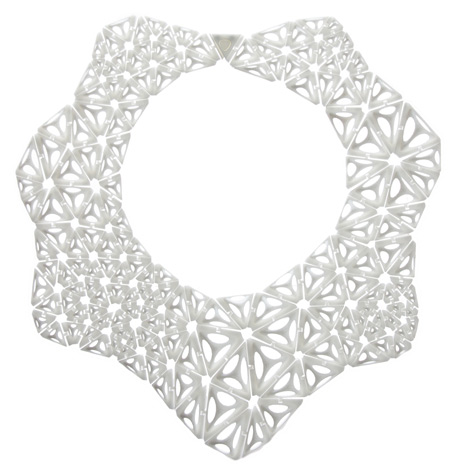
The pair first produced a collection of nylon jewellery derived from the tessellated hinged triangles. The pieces emerge from the printer in a stack of flat sheets but the articulated structure allows them to to fit around the shape of the body.
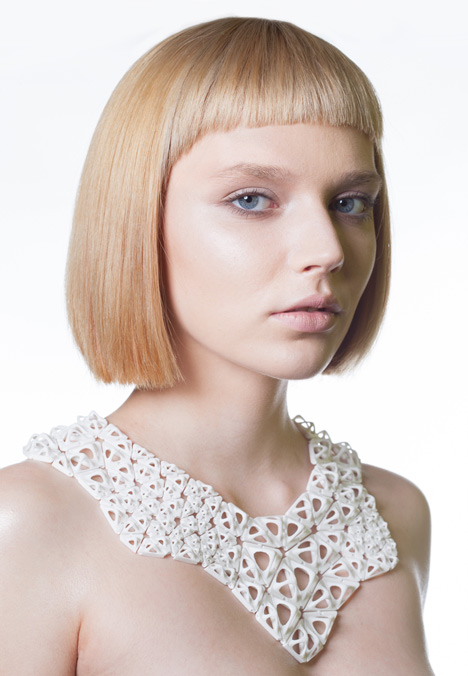
They developed an online application so users can customise the jewellery designs themselves by selecting different module shapes, altering the density of components in selected areas, changing the profile of the design by dragging the outline around, specifying the size and deciding on the colour.
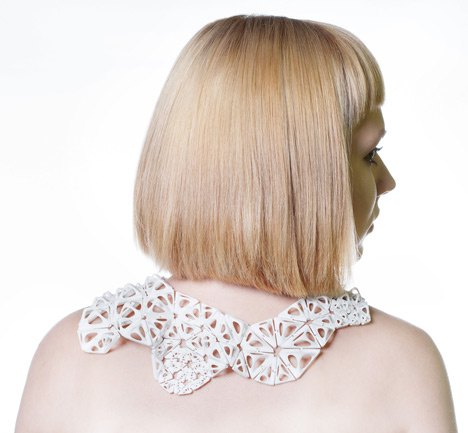
The price of the product is recalculated with every alteration and once happy the customer can order it to be produced by Nervous System. A second free application allows users to experiment with Nervous System's templates and print the results at home.
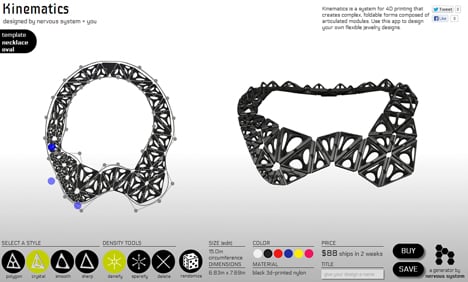
Rosenkrantz and Louis-Rosenberg then developed the principle by adding the ability to fold the design down to its smallest possible spatial configuration. They intend to print their first dress in January.
Photography of the jewellery is by Jessica Weiser.