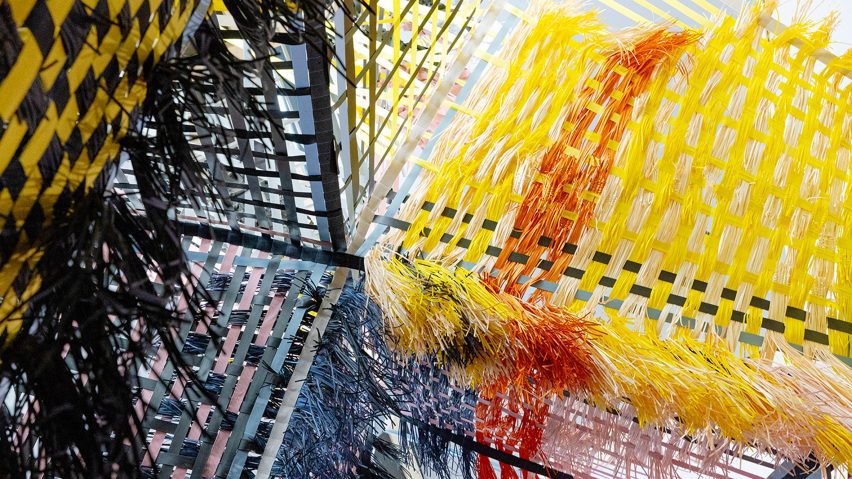
Loom Room shows 3D weaving is "the strongest and lightest construction"
Dutch designer Hella Jongerius has built a large loom in a university building in Eindhoven that was used to create a nine-metre-tall 3D-woven structure, celebrating the craft and creative potential of weaving machines.
Named Loom Room, the installation is a continuation of Jongerius's research into 3D weaving, which she says is "the strongest and lightest construction that we have".

The designer built a loom machine on the second floor of a university building at the Eindhoven University of Technology and the Design Academy Eindhoven campus, which was used to create a cube-like 3D-woven structure suspended in an atrium.
The loom and its nine-metre-tall woven creation were informed by the space around it, with materials draped over aluminium bars hung from the building's structure.
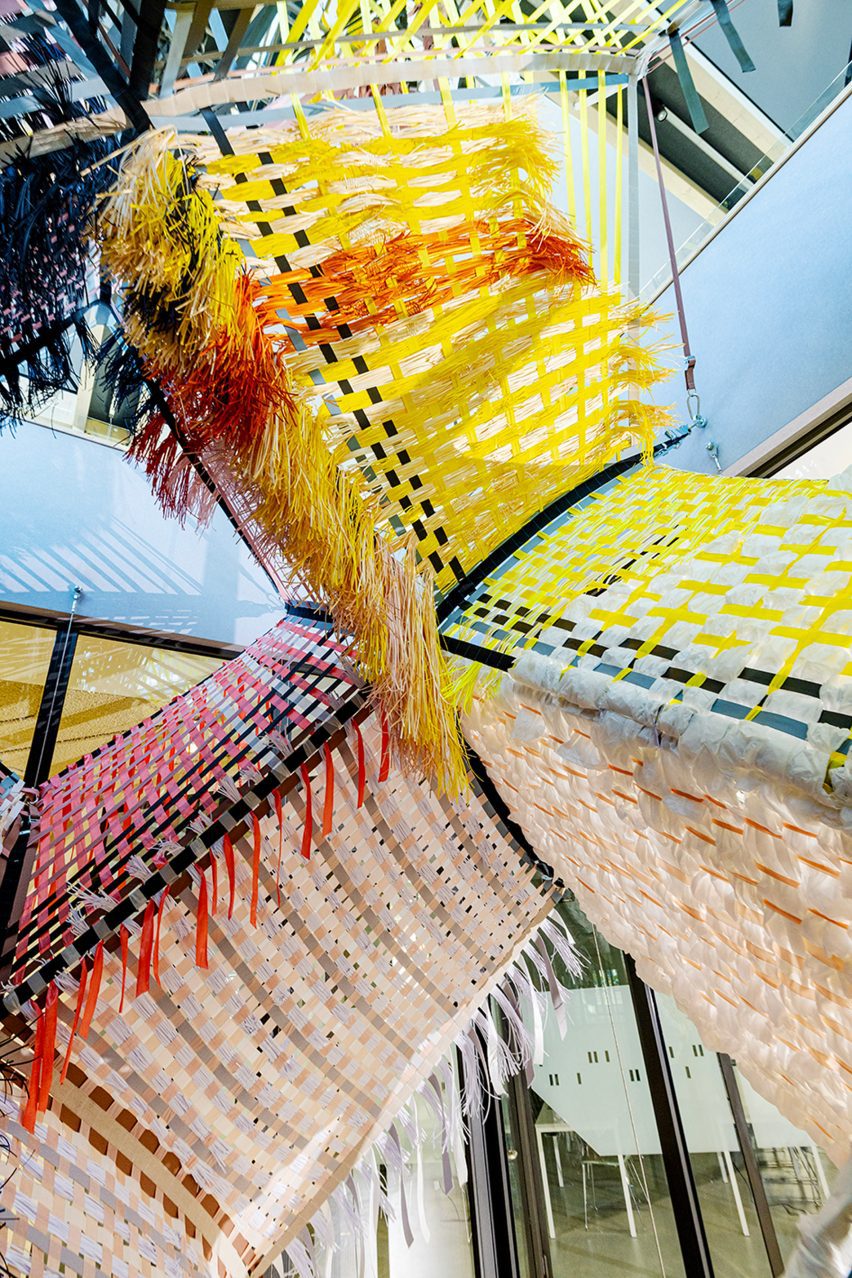
"I thought to make the whole building as a loom and use the beams and the architecture to hang the work in the space," Jongerius said. "The cube was a reaction to how the building looked."
"Now that the loom is ready I can make whatever with the loom – it's not a fixed object," she continued.
"The options are open and that's also what I very much like about designing a machine instead of designing the end product."
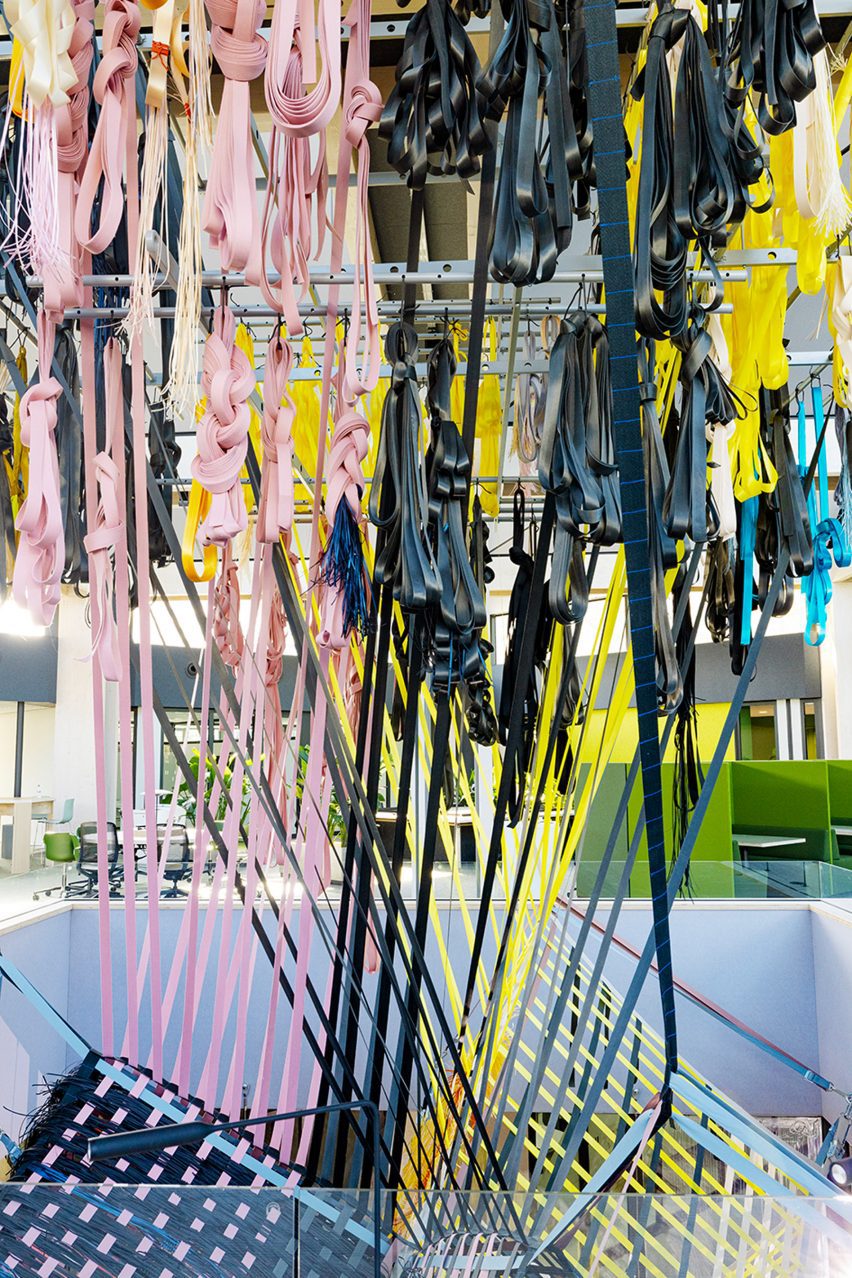
Jongerius used Japanese paper and polyester in different colours, cotton and linen fabrics for the woven structure. This created a soft and tactile installation that was designed to stand in contrast to the concrete modernist university building it is in.
The materials were hand-woven on site over a process of almost two months while the building was used as a study room for students studying artificial intelligence.
"It's the function of art to be disruptive in a space and to challenge the way you look, to take you out of your own brain," Jongerius said.
According to Jongerius, the lightness and strength of 3D woven structures mean they have useful applications in architecture, sportswear and the aircraft industry.
The designer explained that in recent years, the technique has been used to make airbags in cars, as well as aircraft bodies made from woven carbon fibres.
"Lightness in materials is very valuable. There are many ways 3D weaving could lend in our later lives, as soon as we start to fly with our cars, change something in our architecture or work with solar energy," the designer said.
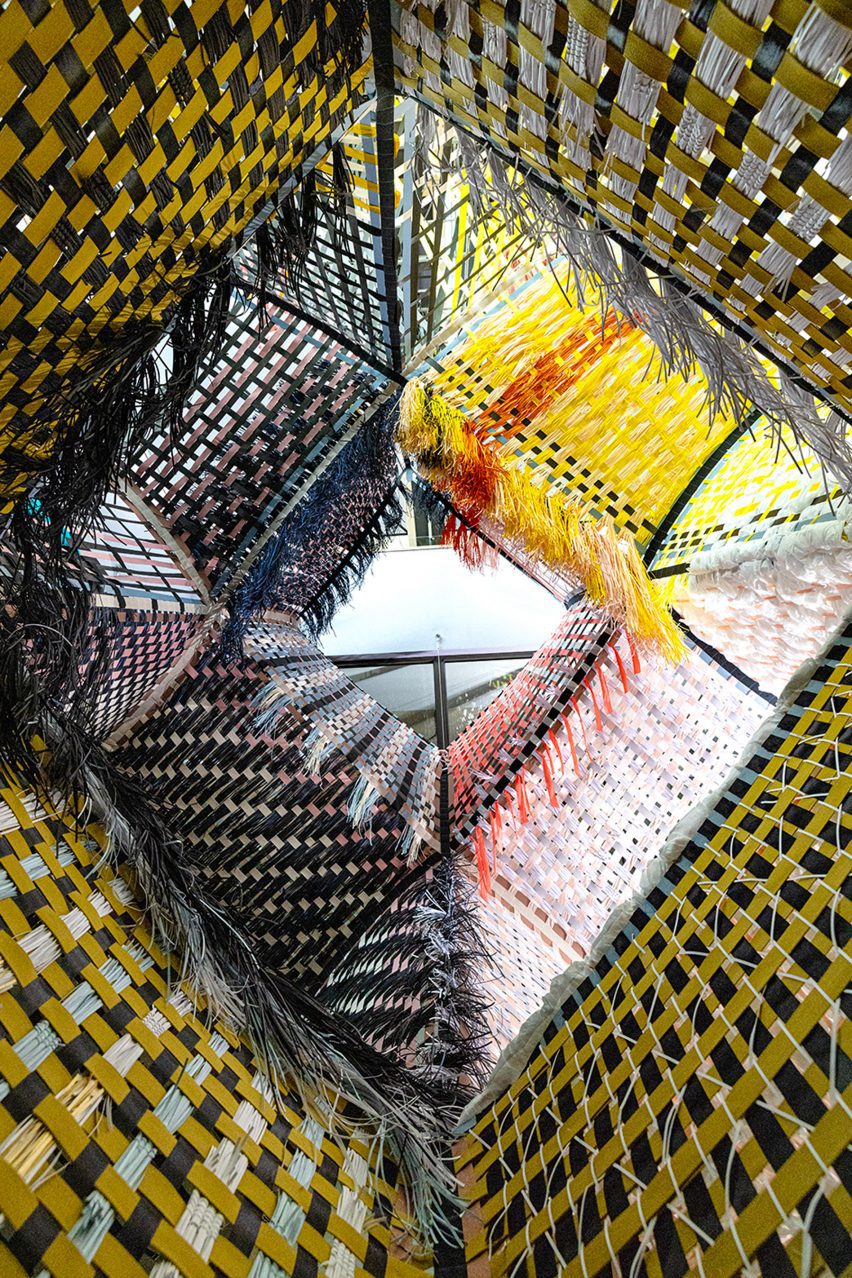
Jongerius argues that innovation in weaving techniques is necessary to keep the craft alive.
She created the Loom Room with the aim of reintroducing weaving machines into the creative process and imagining ways the craft can be innovated for the future.
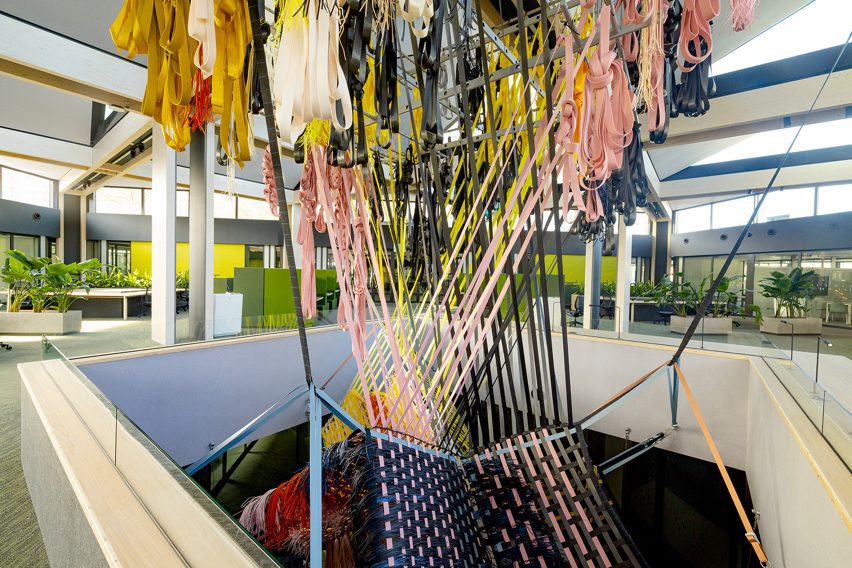
"Weaving is in our culture, in our language, and that's why we have to take it with us to the next technical innovation," the designer told Dezeen.
"If we let this die by commercial entities like fast fashion, then we're losing our culture."
"I'm designing a loom to make it a creative machine again. In industry, they are efficient machines that are no longer creative – it is all about commercial efficiency."
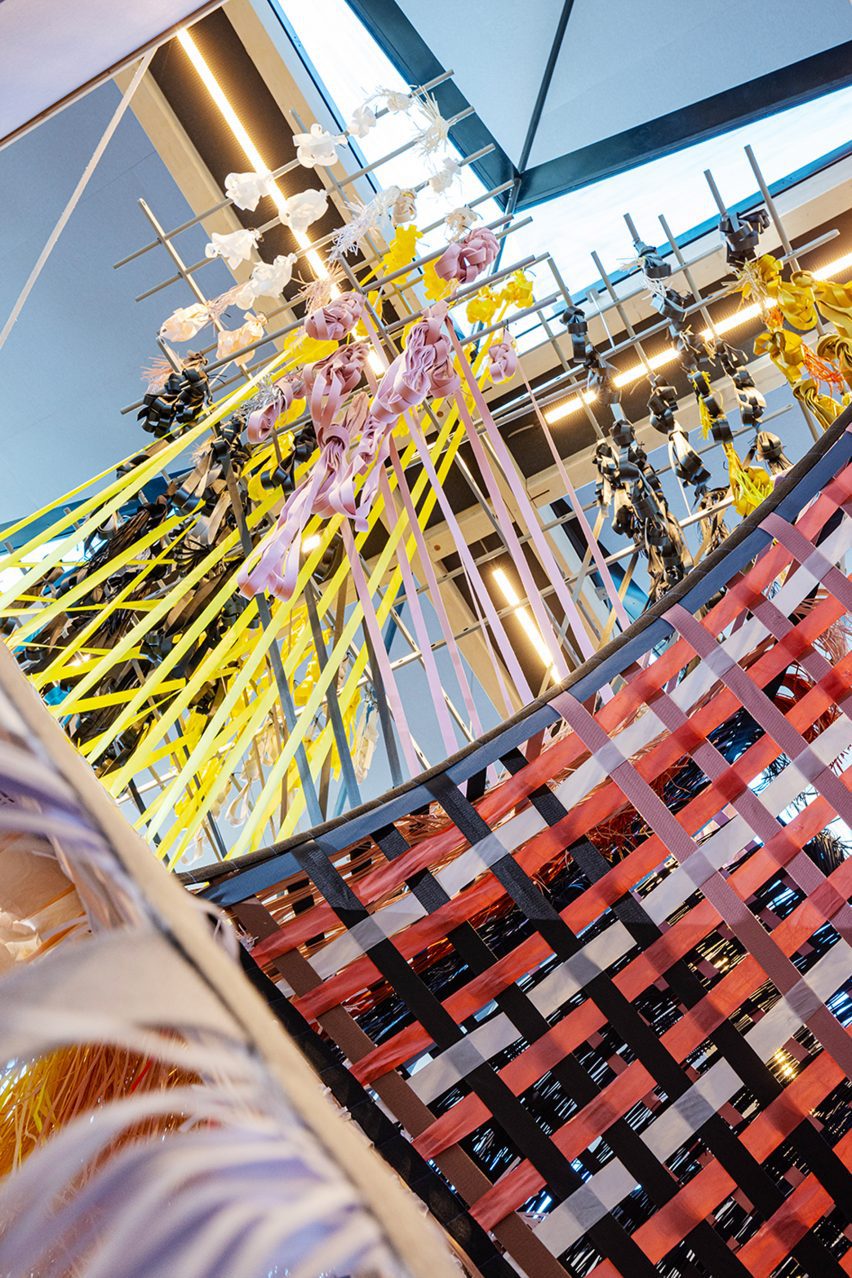
Her method of weaving in three dimensions, which she describes as "pliable architecture", intends to change the hierarchy of traditional two-dimensional warp and weft weaving.
"I changed the hierarchy of warp and weft so the weft sometimes turns into the warp and there is this third angle," Jongerius said.
"I really liked the whole idea of changing the hierarchy of the threads and come with a third thread, which I named the wix – it's a new name for the z angle."
Loom Room is a permanent installation that is open to the public and forms part of Jongerius's ongoing work and research into 3D weaving. Her previous work includes an installation called Space Loom, which comprises a giant loom with 16-metre-long threads hung in a building in Paris.
The designer believes that 3D textiles could eventually replace concrete and cement in construction.
The photography is by Roel van Tour.