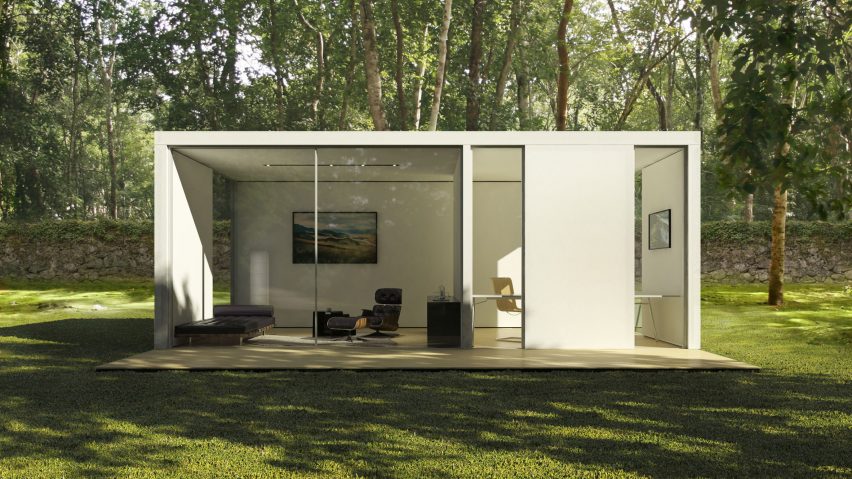
Cover uses computer algorithms to design prefabricated dwellings
A technology-driven home-building company in California says it is "doing for homes what Tesla is doing for the car".
Cover produces customised, prefabricated backyard homes often referred to as accessory dwellings — touted by some as a way to increase density and provide affordable housing in growing metro areas.
The small dwellings can be used to accommodate guests, in-laws or rent-paying tenants, or they can serve as studios, workshops, pool houses or lounges.
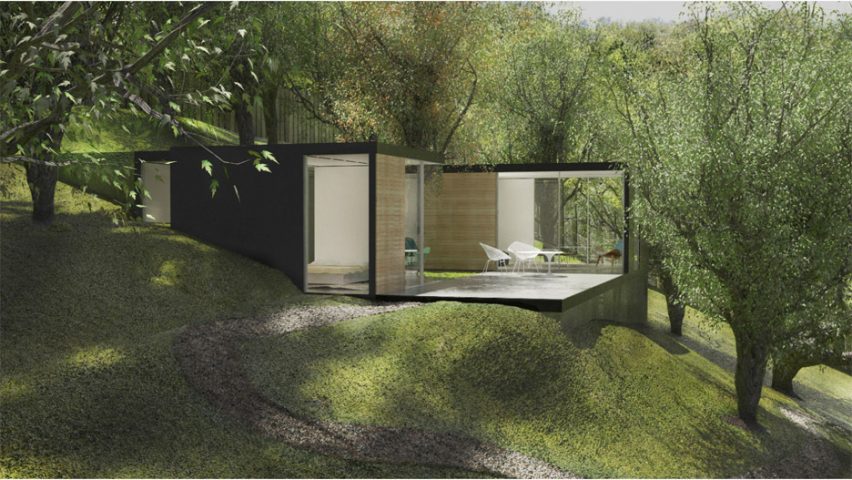
The company was founded in 2014 by Alexis Rivas and Jemuel Joseph, and is backed by venture capital funding. Rivas and Joseph have architecture degrees and formerly worked at design studios.
By using digital tools to streamline the design and construction process, Cover's ultimate goal is to "make living in a thoughtfully designed and well-built home a reality for everyone".
"We're doing for homes what Tesla is doing for the car – using technology to optimise every step of the process, from design and sales, to permitting and manufacturing," the company said.
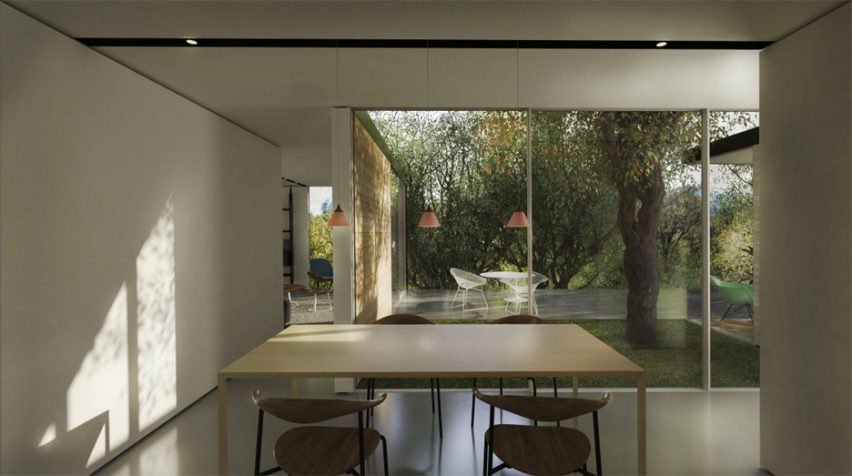
The homes are the latest in a series of projects created using generative design tools, which experts say could transform both the physical world and the role of the designer. The emerging technology uses algorithms to generate every possible permutation of a design solution.
Cover's steel-framed dwellings typically cost from $50,000 to $350,000 (£39,000 to £274,000), depending upon the size, design, location and the client's specific desires.
The average cost per square foot is $250 to $375 (£195 to £292), which is "on par with high-end home construction today". The company aims to make the structures more affordable in time.
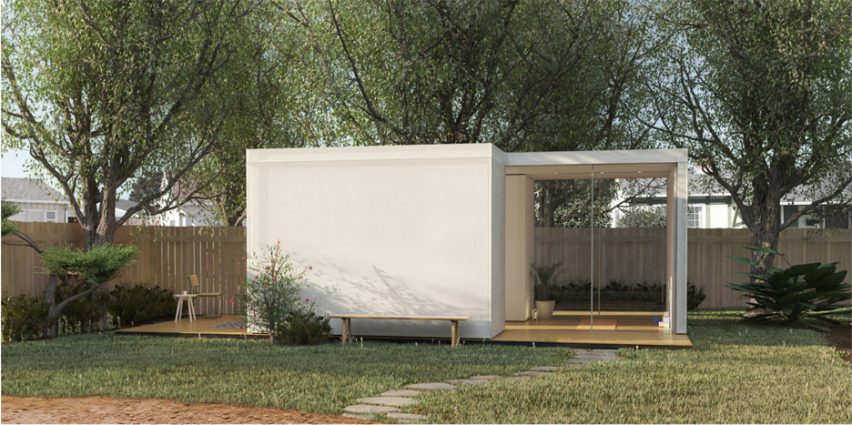
"We will do this by reinvesting profits towards the research and development of an even more efficient design software, building system and manufacturing process," said Rivas in a blog post on Cover's website.
The firm has conceived a three-step process – design, permitting, build.
During the first phase, which costs $250 (£195), clients fill out a digital survey with up to 100 questions, providing information about their lifestyle, design preferences, site details and other topics. The firm also meets with the clients in their backyard to capture additional data.
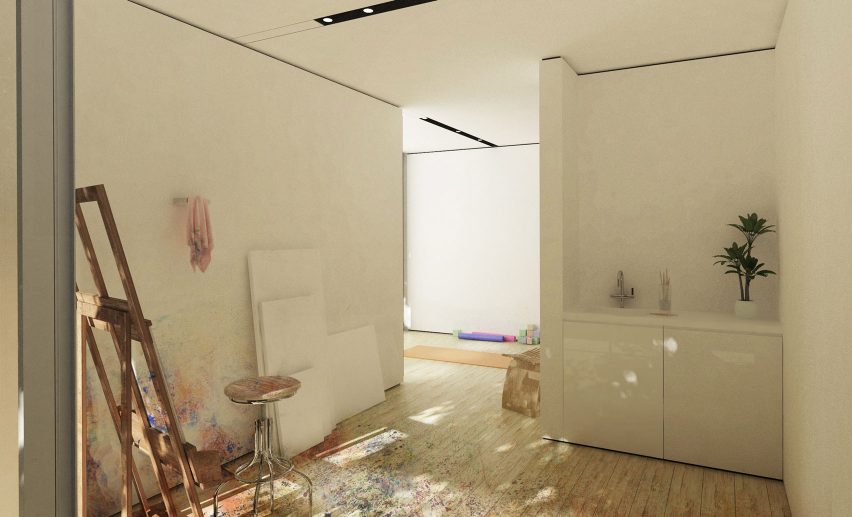
The data is then fed into a proprietary computer program, which generates numerous designs.
The digital program incorporates geospatial data and the path of the sun to help determine wall and window placement. Zoning requirements are also taken into account.
"We use computational design methods to go through hundreds of thousands of design iterations, and select and present the best designs to our clients," the company said.
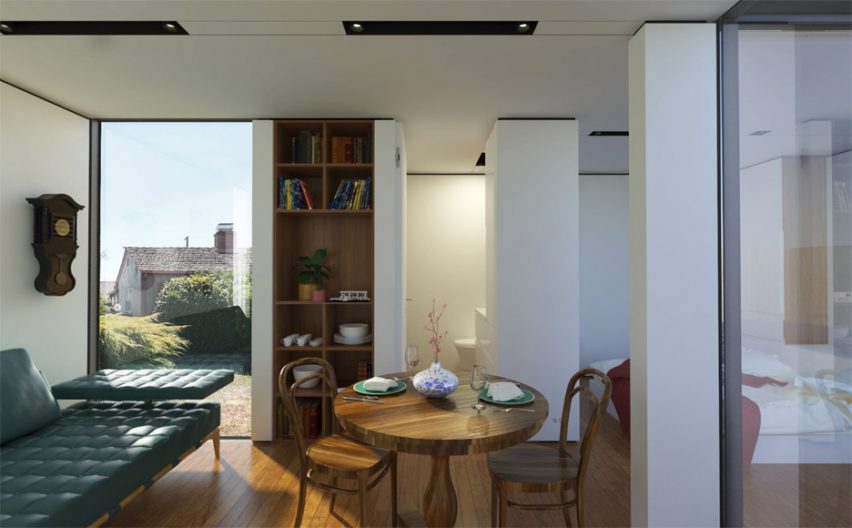
Within three business days, clients receive "photorealistic renderings and plans" and a full quote. During the second stage, the firm obtains the permits necessary to build the structure.
The final stage involves installing the foundation while simultaneously building the home's parts in a factory. The components are delivered to the site by truck and assembled on-site.
"Once we receive approval from the local zoning department, we can manufacture and install your Cover structure within 12 weeks," the company said.
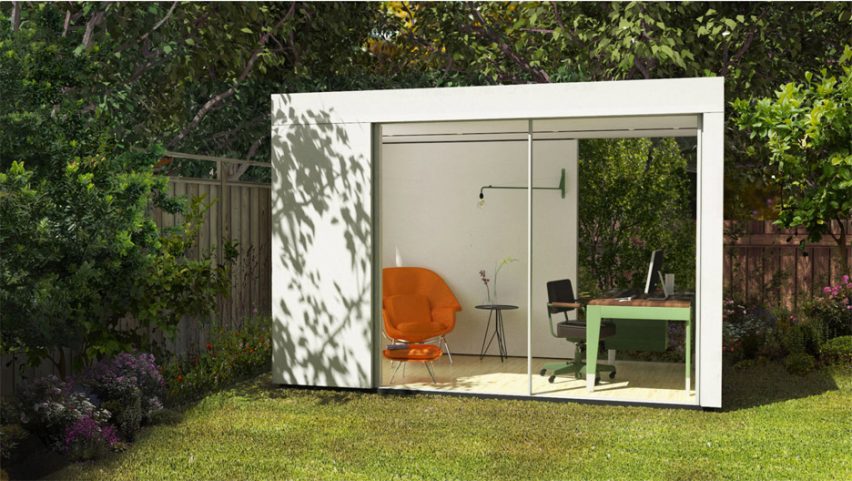
Cover said its homes are more eco-friendly than traditional structures. By moving the construction process into a factory, material waste can be reduced by 80 per cent, according to the company.
Moreover, the company aims to use digital technology to improve manufacturing techniques and produce more energy-efficient structures.
"We're redesigning the details that make up a home to take advantage of the precision possible in a controlled environment," said Rivas. "This allows us to build homes that are 80 per cent more energy efficient than the average new home."
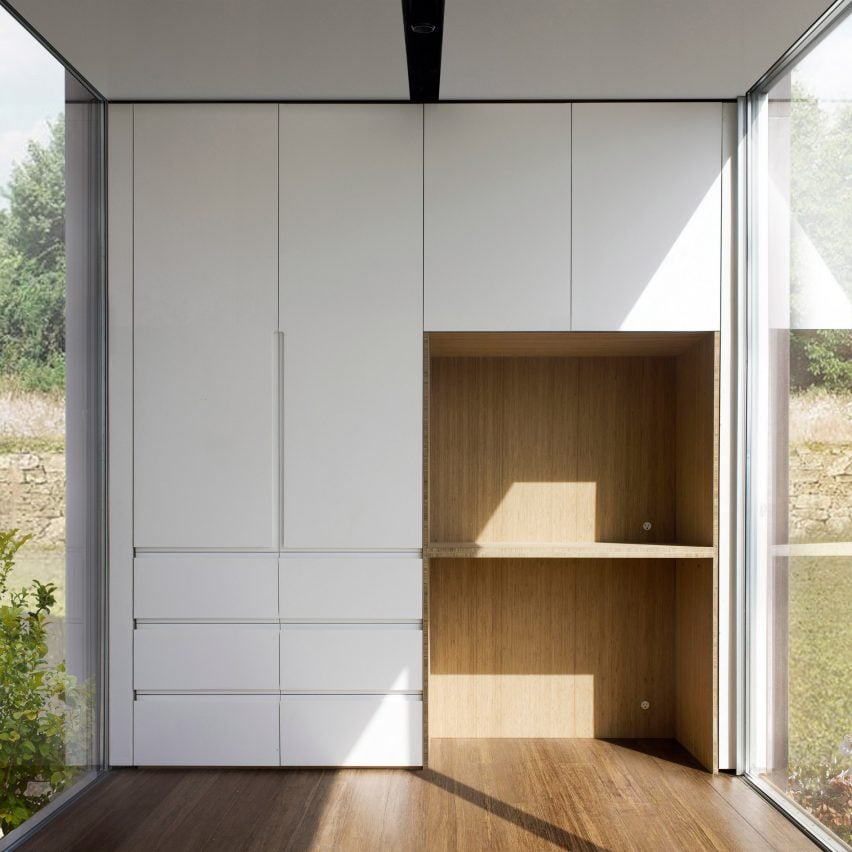
Rivas said the way homes are designed and built has remained largely unchanged in the past century.
"Nearly all homes are still built on-site using stick-frame construction with hammers and nails," he stated. "The design process is more fragmented than ever, with a traditional custom home design requiring the involvement of architects, engineers, consultants, suppliers, general contractors and subcontractors."
"This results in an extraordinarily (and unnecessarily) expensive build process, and makes progress and innovation difficult."
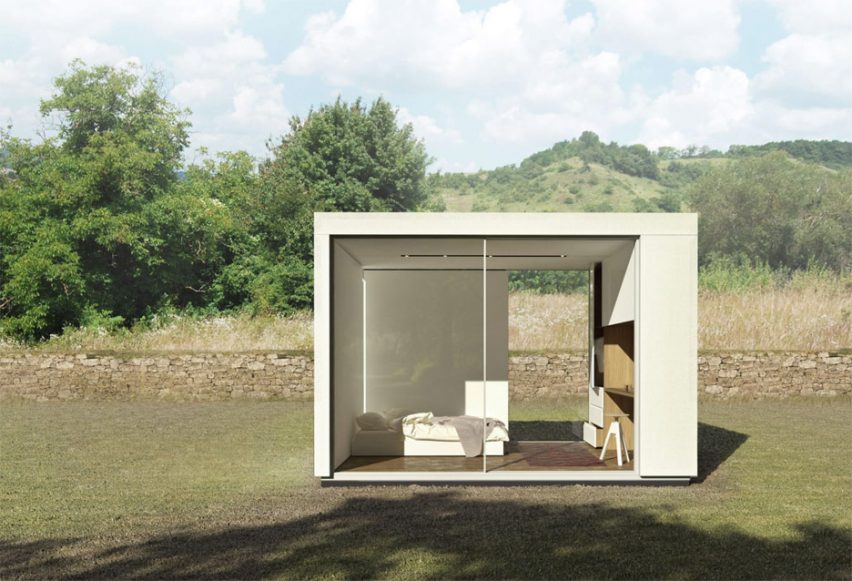
The company notes that it is certainly not the first to "work on a better way of building homes", but its focus on digital tools to optimise the design and construction process sets it apart. "Our approach is different from any other prefab, design-build, architecture or engineering firm that has ever existed," said Rivas.
The structures are currently only available in Los Angeles, although the company intends to expand to other cities.