
Former Apple design director launches mass-timber housing company "to bring productisation to the built environment"
Apple's former design director BJ Siegel has recently established a mass-timber housing company named Juno. In this exclusive interview, he explains how it aims to design housing like it is a product.
Architect Siegel, who worked for 19 years designing Apple stores – most recently as senior design director of real estate and development – believes that Juno can create housing that dispels people's preconceptions about modular buildings.
"If we're going to bring productisation to the built environment for people to live in, that's counter to most people's idea of what an ideal place to live in is," he told Dezeen.
"Typically, architecture is bespoke, bespoke, bespoke – one project to another, there's even a disparity or taboo about repetition within the culture of architecture."
"So we have to design something that is meant to be repeated and that is accepted as higher quality – almost aspirational."
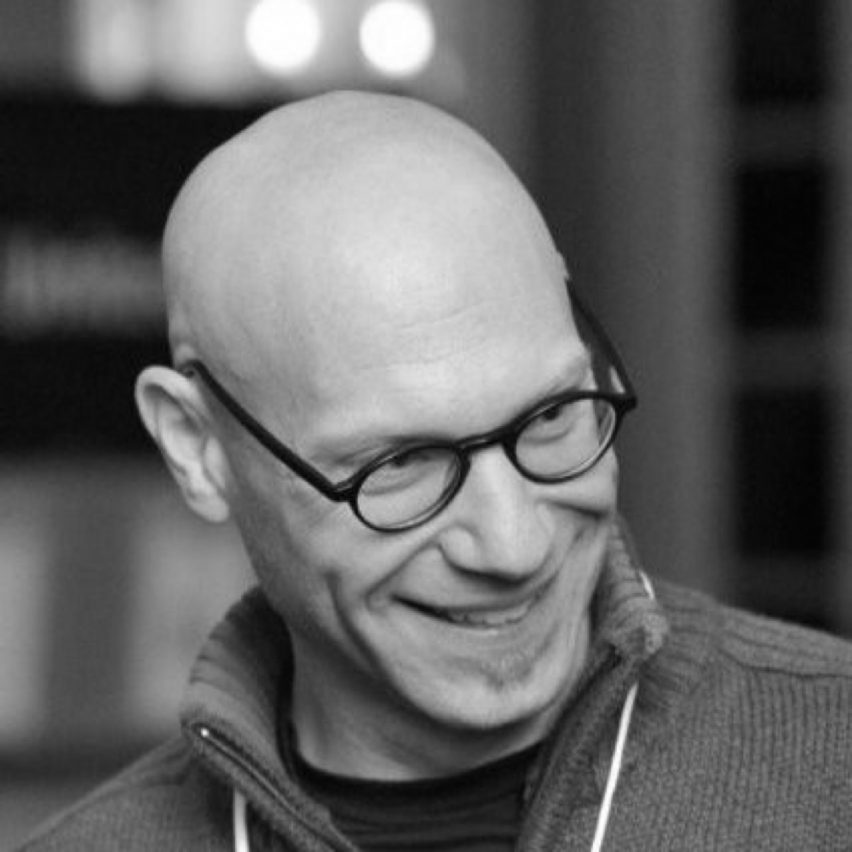
Siegel believes that designing using modular elements will allow Juno to take advantage of design efficiencies and economies of scale while being able to continuously improve the product.
And if the homes are high quality enough, people will not be concerned that they are not unique.
"Taking it from product design, no one cares that your iPhone is the same as the next person's iPhone," he told Dezeen.
"If the quality is so much better, then you're okay that you have the same phone as somebody else," he continued.
Housing built from 33 components
Working with co-founder Jonathan Scherr and New York-based Ennead Architects, Siegel has developed a modular system of around 33 components that can be assembled to create various different housing blocks.
These components are being built in a network of factories across the US, before being delivered, flat-pack, to the site.

"So for us, it comes down to three things," he said. "Design a project that's meant to be built over and over again – design out of components. Number two, set up that third party supply chain such that it's a decentralised supply chain."
"Then number three, provide a set of instructions, a set of tools for people assembling the project."
First Juno project on-site in Texas
Juno has recently broken ground on its first project, a five-storey 24-unit residential block in Austin, and larger projects with more than 100 units are working their way through the planning systems in Seattle and Denver.
The first developments are being delivered at "market rate", but Siegel believes that as more developments are built, the savings from mass production will allow them to reduce the cost of the housing.
"We are starting at a goal of providing a much higher quality product to the market at a faster timeframe than conventional – we're seeing great gains in speed already," he said.
"And we're delivering it right now at market rate, just right out the gate at market rate. And then over time, that cost will continue to go down."
Housing will be mass timber above podium level
All of the housing will be built from mass-timber above a podium that will be adapted to each of the project's sites.
This will not be cross-laminated timber (CLT) – the most common type of mass timber – and Juno is not revealing details of the material at the moment, although it will be manufactured in the US.
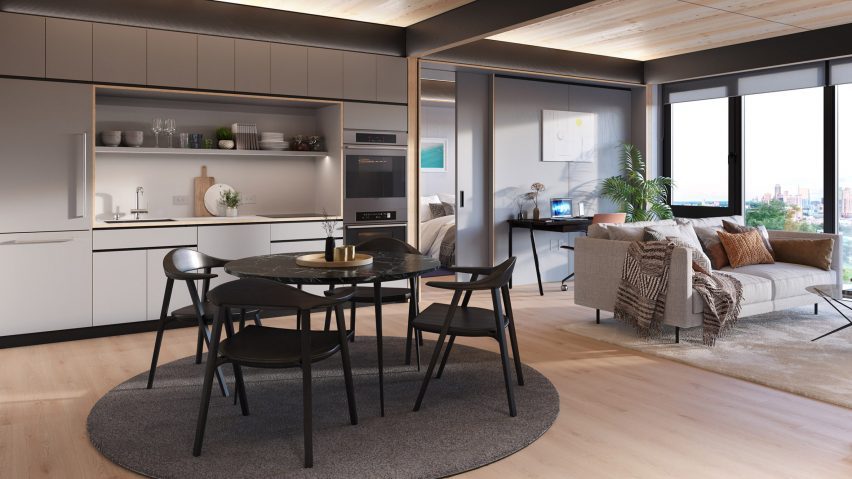
"We are not using CLT," said Siegel. "We are actually using another variety that we think is slightly better than cross-laminated timber for a number of reasons."
"The one that we've picked is not as widely available as cross-laminated timber," he continued. "And as a result, there's a slight advantage to being able to use it that we've discovered. We feel that we're actually using a lot less material."
Read the edited interview with Siegel below:
Tom Ravenscroft: Can you tell me a little about how Juno began?
BJ Siegel: Before working on Juno, I spend about 19 years working on the Apple retail store programme. Back in 1999 is when I kind of started working on projects at a small interdisciplinary design firm here in San Francisco. We were actually doing tradeshow work for Apple, the Macworld Expo stuff, and we got the opportunity to think about how Apple would bring their brand directly to the consumer.
So we spent a bunch of time coming up with the first concepts for the Apple stores. Long story short, I did that for about eight years, and then in 2009, got asked to work properly directly as head of AI innovations and standards. Then, within two years, as the head of design for Apple on their projects across the world.
Four major things that came out of that. First how to design a product that people really get emotionally connected to – that was a big thing at Apple.
Number two, work on continuous improvement to really understand how architecture can be more like product design, and really focus on the customer – continue to improve through feedback and innovation, not just using one-off projects.
The third is Apple really challenged us to think about the way we deliver the project more like the way they deliver products through a kind of owner-furnished direct source supply chain model.
And that actually spurred a lot of investigation as to how to translate that work from a product into this industry, which is really kind of not focused on that.
So that really was a big, big focus.
And then the last one was really a commitment to the responsibility of the building to its environment, I think that was, you know, in the second half of my time at Apple that became a big deal.
Tom Ravenscroft: How did this experience inform Juno?
BJ Siegel: Those four lessons were kind of primed in my head, as I was deciding to take off after 19 years of working on Apple. When I met John, the other co-founder, we realised that the customer, the end-user, wasn't always a consideration in developer housing.
So we set out to think, can we design a much better, higher quality product, a product that really focuses on the environment, and addresses the needs of the users and matches our own values.
So the question ended up being how do you design a product that's higher quality, but not deliver it at price points that people can't afford, because typically higher quality, higher environmental impact comes at a price premium.
For us, the kind of the generative idea was delivering that higher quality product at a more approachable and achievable, more accessible price point for folks.
And that's where we started really diving into technologies, processes, you know, things that we could do. What can we do in the background, to really make it possible to deliver it that way. The customers that live there don't really mind or care about how you got there, but they do care about what it costs and if they can afford it.
So all of the business models that we've created in the background is there to serve this better quality product.
Tom Ravenscroft: Can you give me more detail about the business model?
BJ Siegel: If we're going to bring productisation to the built environment for people to live in, that's very kind of counter to most people's idea of what an ideal place to live in.
Typically, architecture is bespoke, bespoke, bespoke – one project to another, there's even a disparity or taboo about repetition within the culture of architecture. So we have to design something that is meant to be repeated and that is accepted as higher quality – almost aspirational.
So taking it from product design, no one cares that your iPhone is the same as the next person's iPhone. If the quality is so much better, then you're okay that you have the same phone as somebody else.
So you've got to design something that relates to people's values, feels higher quality, higher craftsmanship, it relates to the things that people would aspire to, but it can't be priced out.
We're looking at middle-income, market-rate housing. This is for people who have everyday jobs. And so how do you deliver that kind of aspirational product at a price point. And so the first thing that we really did was decided to look to see what were the smallest number of parts that we could design to actually keep the skew count low, keep the quality really high.
And then take those very small number of parts to build a supply chain around delivering those parts to our project sites. So that we could put these things together.
And those parts are made such that they can live independent of each other, they can be second or third sourced if need be, we can always chase the best technology, the best vendor who's doing the best work, we can learn from their techniques.
We then take those parts, make them very predictable, make them relate the same way every time they're using the project, and then allow a lot of flexibility in creating many, many different buildings on different sites.
Then make it such that the assembly of the project on the site is really like a factory assembly line, but it's on a construction site. So you've really simplified down, potentially, the assembly of the project because much of it is done ahead of time.
So for us, it comes down to three things. Design a project that's meant to be built over and over again – design out of components. Number two, set up that third-party supply chain such that it's a decentralised supply chain.
Then number three, provide a set of instructions, a set of tools for people assembling the project.
Tom Ravenscroft: And how does timber fit into that?
BJ Siegel: Timber is really quite important for us. We started out by wanting to take advantage of new technologies and be more manufactured than constructed. We also wanted low labour, high machine, high technology in their manufacturing.
And finally, what does it contribute to the sustainability of the project? What we discovered very quickly, as we were doing our design work, was that we wanted to focus on mass timber.
In the United States, it's a slightly new conversation. It's a much older conversation in Europe.
But you know, you look around you do your research, you learn from everybody that's done something in the past. And so for us, mass timber was coming online in the United States – the building code was changing.
For us, mass timber was key to unlocking a lot of benefits. It's a material that has many advantages. We found one that we think is highly advantageous – low waste, highly manufacturable, highly strike-strong in its strength compared to other mass timber.
Tom Ravenscroft: Is it cross-laminated timber that you'll be using?
BJ Siegel: Well, no, we are not using CLT. We are actually using another variety that we think is slightly better than cross-laminated timber for a number of reasons. The one that we've picked, is not as widely available as cross-laminated timber. And as a result, there's a slight advantage to being able to use it that we've discovered. We feel that we're actually using a lot less material.
I can't say what it is right now as we want to keep our advantage. But I can say it's a mass timber manufactured in the US.
Tom Ravenscroft: So you are expecting to get much of the benefits associated with CLT, plus some additional ones?
BJ Siegel: Yes, and it's worth mentioning that by using mass timber and the way that we are using it, we are finding a very significant advantage over other materials that can build tall projects like concrete or steel. As a result, we're building much lighter buildings. The mass timber that we're using is coming from a responsibly and responsible forestry practice environment and as a result, it actually is being considered a negative contribution to carbon from a biogenic resource.
As a result, we are finding ourselves in an embodied carbon situation that is quite unique, actually. And quite advantageous.
Tom Ravenscroft: So all of what you've described sounds similar to what others have strived to achieve. What makes you think that you've got the secret sauce to do what others have failed to?
BJ Siegel: The process of trying to productize homebuilding has taken place since the 1940s. This is not a new thing. And a lot of architects get into this and try to figure out what's the recipe.
And a lot of folks have come up with some really great ideas that just haven't worked. There were a lot of things that we learned and watched. Our system, first and foremost, tries to learn from the lessons of the past.
We have only one volumetric component, which is our bathroom, everything else is panelized, flat packed, and shipped very efficiently. And some very large companies have invested in fabrication and placed a real emphasis on vertical integration – companies would buy up architecture firms, general contractors, their own factories. Asset intensity was unable to be sustained.
So, one of the things that we're really focused on is this idea of instead of being vertically integrated, we're really very focused on being vertically aligned. And that was a mission right from when we first started the company – vertical alignment with amazing partners. So we are not setting out to be everything.
In fact, we're like the orchestra conductor, we are actually bringing together people who don't typically work on these kinds of projects. And we're trying to bring this amazing resource, this amazing skill set together, great fabricators who build parts; they're kind of becoming part of this ecosystem.
So I think that is a stark difference to the way a lot of folks have approached this problem, we are ending up being very asset-light, we can be very nimble, we can follow the best technology, the best techniques, we can get competition within the supply chain, and continue to really chase the best ideas, always listen and learn and be humble that way.
Tom Ravenscroft: And is this theory being put into practice?
BJ Siegel: One of the things that we'll announce next week is that we have broken ground on a first project in Austin, Texas. It's a five-storey 24-unit project. And we actually have a couple of other projects in our pipeline already under control and moving forward. Much larger, much larger projects, eight to 12-storey projects in Seattle and Denver.
And really, that's where we're going to concentrate our efforts in these kind of 100 to 300 unit projects, eight to 12 story projects.
So you are operating in the real world, not theory?
BJ Siegel: We're not aspirational in that way. We are actually doing everything we're saying. And actually, everything that we're building is compliant with today's codes.
We don't have things that we're dreaming will happen. We have real projects with real general contractors, real investors, real component fabricators who have actually built the real parts for us.
We've built full-scale mock-ups of the one residential unit. We've studied all of the assembly with the installers and the fabricators we've actually used, we have a team of continual like data collection experts, so to speak, watching and learning so that we continue to feed that back into our process and get better and better.
Tom Ravenscroft: So you're happy to work within the current building system?
BJ Siegel: We want to make living sustainably easy for people. We want to actually create the first network of mass timber. Kind of a net-zero carbon contribution from the embodied carbon standpoint, which is highly unique. In fact, our environmental engineers that we've been working with have told us that they've actually never seen anybody getting to this point in the embodied carbon category.
You know, our operational carbon is 20 per cent, better than the most stringent codes in the United States right now. So we are, we are leaning in, we're not there yet. We're on a journey. We're not telling people we are net-zero, because that would be silly. It's a journey. And it takes a lot of effort. Especially in housing, it's a place where there's not a lot of investment just for the sake of making statements like that.
We're trying to build in the most responsible way, in today's context. And we're trying to bring a whole network of these projects to a lot of people, and not make people change the way they live in order to be able to live in a sustainable way. We're actually going to start with today's goal and get better as we go.
Tom Ravenscroft: Then I suppose the way your system's built, if codes change, you can adapt and amend?
BJ Siegel: Absolutely, it's meant to have continuous improvement components, one of the beautiful things about the components is that they're independent of each other – there's a very small number of components, maybe like 33 components that make up every part of the residential part of a project.
The podium will be very unique for each site, with a different programme, different foundation, etc. and a fairly conventional podium.
Tom Ravenscroft: And above that, you will have the modular residential housing?
BJ Siegel: Yes. And really, it's meant to be where we exploded with our efficiency, and the quality of everyday life. That's really where we want to focus. When people walk through the front door of the unit, they're going to look at it, hopefully see craftsmanship, light, air, materials, the volume of space that you can't find in a developer housing – an emphasis on the everyday life, not just the list of amenities, but where people actually spend their time.
Tom Ravenscroft: So you've got big aims and ambitions for Juno?
BJ Siegel: Not big aims for the sake of just big aims, but big aims for making a contribution. So we're on a trajectory with the Austin project. We are self-developing, we are the developers. The next two projects, the ones in Seattle and Denver, we're co-developing with local co-developers. Then we will continue to reach further towards other developers.
We're starting by eating your own dog food, so to speak. We're proving it to ourselves, and everybody else. And then as we grow, and as we do bigger projects, and more of them, we start reaching forward, sharing up development tasks with others. Then we start using that as a service and a platform where others can choose to help us deploy our product, really, because it is more like product design at that point where the investment of R&D, the investment of tools, and processes, which we've proven out, and we'll have a track record, we can start getting more and more interest from the development community.
And then every time we do this, you know, we get better, we learn more about what happens, we collect the data, we build more partnerships with more people. And at that point, you know, you start adding scale to the matrix and scale reduces cost, you start adding repetition of partnerships, and that comfort level helps to kind of continue to reduce the cost.
So we are starting at a goal of providing a much higher quality product to the market at a faster timeframe than conventional where we're seeing great gains in speed already.
And we're delivering it right now at market rate, just right out the gate at market rate. And then over time, that cost will continue to go down.
Tom Ravenscroft: So you're working within the real-world constraints of each project?
BJ Siegel: Yes, the projects themselves are funded with conventional construction development capital. Not funded by venture capital.
Tom Ravenscroft: What do you think will be the biggest obstacle to this actually upscaling into something that is viable across the whole United States?
BJ Siegel: Well, first of all, because of this decentralised supply chain, if we chose to be global, we could do that. We could build supply chains in other countries. And we could apply this thinking to other places. That is not a constraint.
We believe in focus, we have one product right now. And I think that's another area where folks have failed in the past, where they've tried to do too many things at one time.
So we have one product right now, market rate, multifamily housing. We can choose to go into other verticals; student housing, elderly, housing, hospitality, but we're really being focused right now.
I'd say there are two things that are road bumps, but not obstacles. One is time because it's different from a product company or software company, the cycle time is longer to do a project.
As a result, you have to be patient enough to allow it to get through regulatory approval processes in places like Seattle, which is very slow. It has nothing to do with how fast we work, it's to do with the city. It's just reality, right?
So time, we have to be patient enough to get it done.
I think the second thing is that some folks that are just a little less excited to be innovative, they're really a little bit more risk-averse. And so for those people in that chain, a lot of the benefits come after seeing one or two of these happen.
In order to get the full benefit of the process. You've got to demonstrate a couple of times and so that patience that I mentioned to you, we have to be patient. Not everybody wants to be an early adopter.
So that kind of scale has to come once you can demonstrate to people who want to see first and get involved second, but we've gotten so many people who have said to us, we are so excited to get on this bandwagon, but we just don't want to be first.
So that's okay, we'll find a couple of people who want to be first with us, and we'll do with them, they'll probably benefit in the long run more, because they've been part of the beginning.
Renders are by Engraff Studio.