
Prometheus Materials uses algae-based cement to make masonry blocks
Colorado-based Prometheus Materials has developed masonry blocks from a low-carbon cement-like material grown from micro-algae.
The blocks, which meet the American Society for Testing and Materials (ASTM) standards, were made using an organic cement-like material grown in bioreactors that reproduces itself in ways similar to coral.
"Coral reefs, shells, and even the limestone we use to produce cement today show us that nature has already figured out how to bind minerals together in a strong, clever, and efficient way," said Prometheus Materials co-founder Wil V Srubar III.
"By working with nature to use existing microalgae to bind minerals and other materials together to create new types of sustainable biocomposite building materials, we can eliminate most, if not all, of the carbon emissions associated with traditional concrete-based building materials."

This bio-cement was made from biomineralizing cyanobacteria that are grown using sunlight, seawater, and CO2.
The blocks were created by mixing this bio-cement with aggregate to create a low-carbon building material with mechanical, physical and thermal properties comparable to portland cement-based concrete.
The bio-cement could be mass-produced as an alternative to portland cement, which is a huge source of carbon emissions as it relies on clinker made from crushed and burned limestone. The process separates the calcium, which is a key ingredient in cement, from the carbon, which is released into the atmosphere.
"You can't just simply decarbonize fossil fuels, change fossil fuels," said Prometheus Materials CEO Loren Burnett.
"You've got to decarbonize building materials," he told Dezeen. "Building materials are a huge problem from a CO2 perspective."
The company is using existing facilities in order to harvest the biomaterials necessary to create the blocks.
"There are some major facilities that are already in place that were put in place for the biofuels industry several years ago, which are at this point dormant but available," said Burnett.
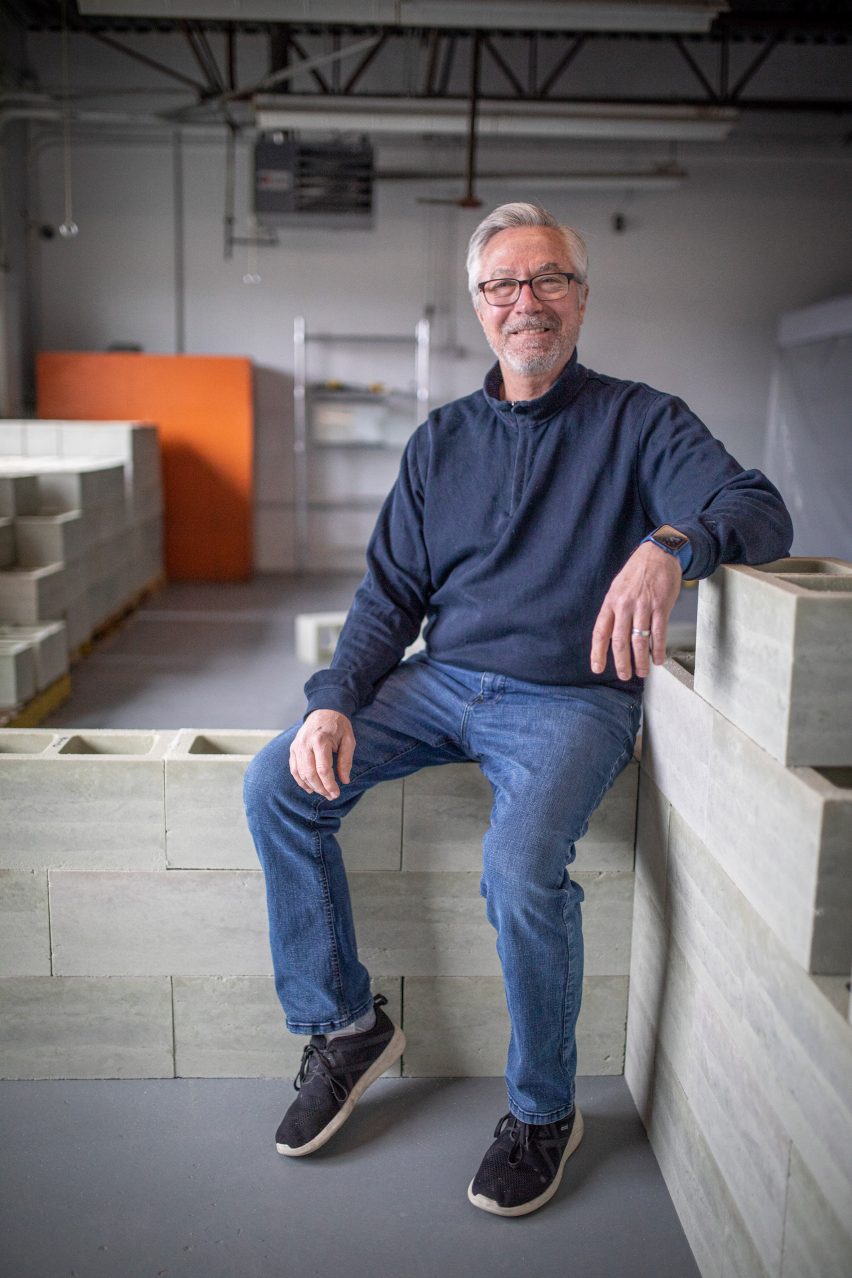
The material was first developed by University of Colorado at Boulder (CU) professors in response to a call from the US Department of Defense to envision sustainable materials. Prometheus Materials was established in 2021 to make the material available for public use with masonry blocks being the first application.
Since it was established it has received funding from the Microsoft Climate Innovation Fund, European venture capital firm Sofinnova Partners and global architecture studio SOM.
SOM's involvement came on the heels of a prior relationship with co-founder Srubar, who won a fellowship from the SOM Foundation in 2006. The studio that designed the Burj Khalifa, which has a concrete structure and is the world's tallest building, and has previously invested in research into low-carbon materials.
"[SOM] use[s] a lot of concrete and cement and they are very aware of the need to decarbonize the process," said Burnett.
When asked if some of the advances in concrete that have allowed for taller and taller skyscrapers to be built could be repeatable Burnett said that the biocomposite masonry will match and exceed the capabilities of portland cement-based concrete.
"Because we are a different material, we actually enable new products to be developed and used that would not be available using traditional concrete," he said. "We are an alternative material that has additional capabilities."
The material is going through testing in the Colorado city of Boulder and will go through the American Society for Testing and Materials (ASTM) protocols later in 2022.
The company has plans to create a precast material for roofing tiles, wall panels, sound barriers, and other concrete elements in the next two years.
Algae and other biomaterials have been proposed for a variety of uses in the design industry. Earlier this year, Natural Material Studio and Frama presented terracotta materials made from algae.
Other research into sustainable replacements for modern building materials includes an MIT initiative to make tree forks stand in for load-bearing steel.