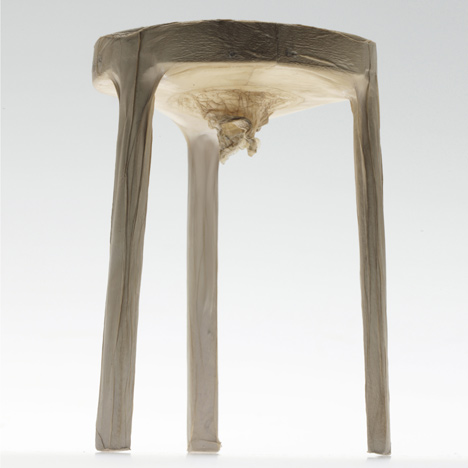
Xylinum by Jannis Hülsen
Berlin designer Jannis Hülsen upholstered this stool by using bacteria to grow a cellulose skin over its surface.
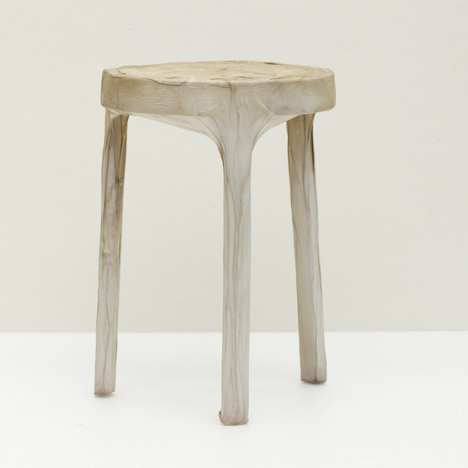
Called Xylinum after the bacterium used to create it, the furniture is immersed in a tank while the bacteria consumes sugar and builds a cellulose fibre structure.
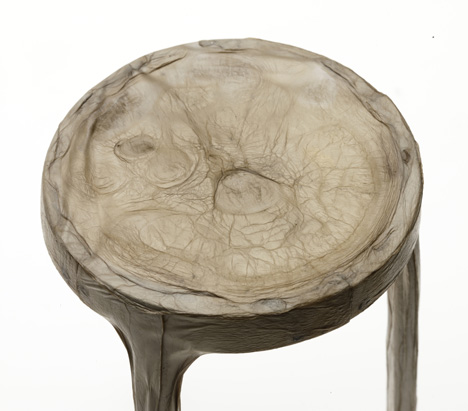
Once finished it can be dried out to form a material that's 100% biodegradable.
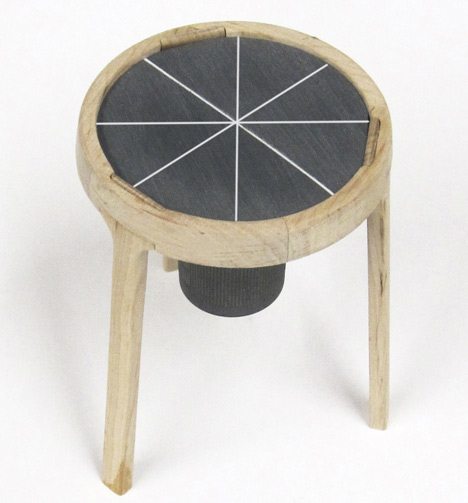
Here are some more details from Jannis Huelsen:
Background
Xylinum is a research project that asks: “What could future materials and production processes look like?” It has been known for a long time, that micro-organisms can be used for industrial processes, like yeast cultures for production of bread, alcohol or cheese. Since it is possible to decode the DNA of organisms, and even to change it consciously, the so called “White Biotechnology” has changed fundamentally. Now it has become possible to replace chemical by organic processes. This already has happened in the textile and detergent industry and shows big potential in the production of energy or plastics. Bacterial-cellulose is such a material, which is produced by a bacterium called Acetobacter Xylinum. In a nutrition liquid it transforms sugar into a cellulose-fibre structure. The project was realized in collaboration with the company Jenpolymers in Jena, which developed the technique that makes it possible to shape the material already during the production process inside the liquid.
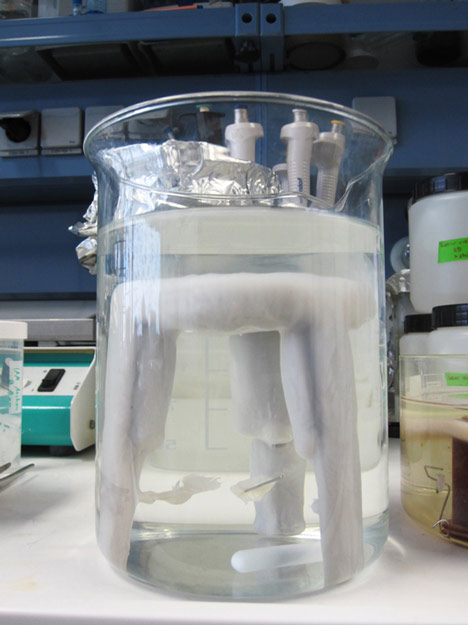
Production
The properties of the cellulose fleece are adjusted to its medical use. So far, applications are hollow implants for bypass operations or as wound dressing. It is characterized by its three-dimensional nano grid structure, which leads to excellent mechanical properties. Its stability in a wet condition is even comparable to steel or Kevlar. Moreover, it is so pure that, if placed inside the human body, it is settled by the body's own cells. Therefore, it is non-allergic and fully recyclable. Due to the fact, that the material is made for a medical use inside the human body and on wounds, the material binds a lot of water and needs to be dried afterwards.
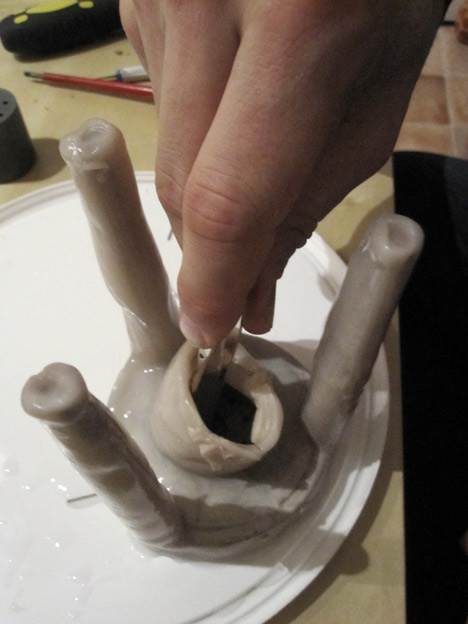
A pivotal question of the project is how to process and use the material. To sum up the many different material samples that originated from the project and to make the material available to the public, there is a book called “Bakteriencellulose-Bebilderter Erfahrungsbericht einer Diplomarbeit” (“Bacterial cellulose – illustrated report of a diploma thesis”).
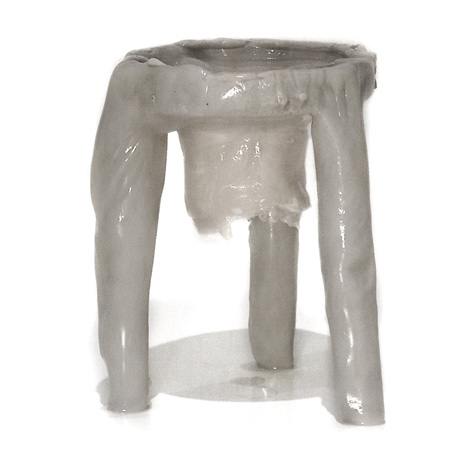
Creation
The aim of the project was to create a blueprint for new materials and production processes. A stool meets the properties of the material and it has a clearly defined function, while providing a projection surface for the material. Due to its skin-like appearance, the cellulose material shows similarities to materials such as leather or parchment, which have a long tradition in furniture production.
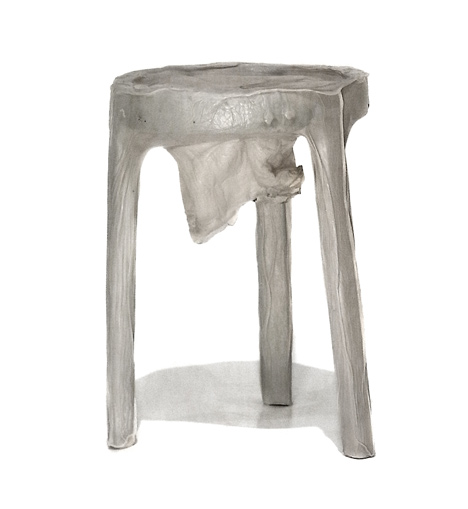
Thus the handling of parchment for furniture is one of the most sophisticated and expensive crafting techniques. The material fills the seating surface functionally, only thus turning the object from frame to stool.
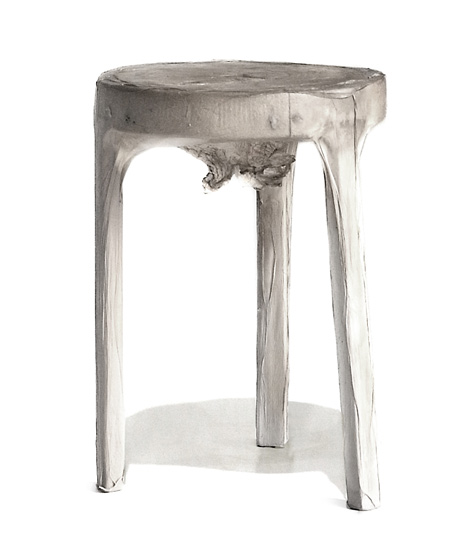
The design is based on experiences from various experimental material samples. Since neither the aesthetics nor the behaviour of the bacteria could be foreseen, the project turned up with many surprises. For example, the material with the best qualities for the bacteria coating turned out to be wood. Being natural cellulose itself, it turned out to be an appropriate material for the frame construction.
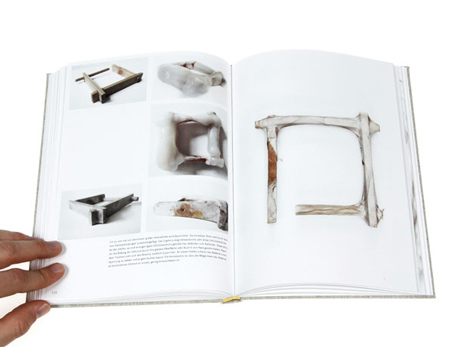
Alder wood was chosen because of its fine and regular structure and drying properties. The connection between ring and legs are form-fit and are provided with radii, to prevent the material from being damaged. To make sure the connections stay stable after the construction is removed from the liquid a special glue, that reacts well to the bacteria had to be used. For the final coating the ring was filled with a mould, that could be removed after the coating process.
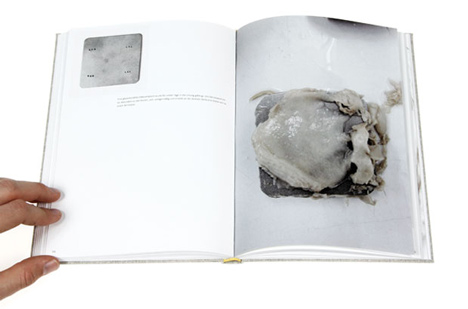
Evaluation
The stool shows an attempt to integrate natural, unpredictable processes into a planned design process. It is possible to plan the construction and the material, but neither to predict the shape after the drying process, nor the eventual appearance of the cellulose.
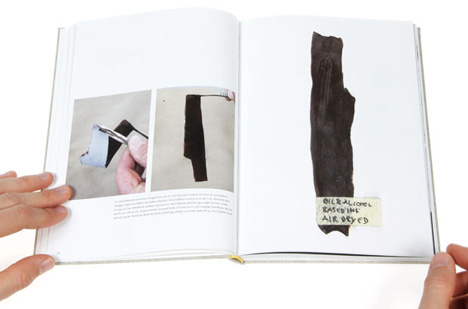
The new way of production in a nutrition liquid, using micro-organisms, places consumer goods in a new context. In contrast to exhaust-producing factories, a new generation of products could be produced in a natural way, compared to a sprouting seed or a growing being. The unique look of each stool supports this characteristic naturally.
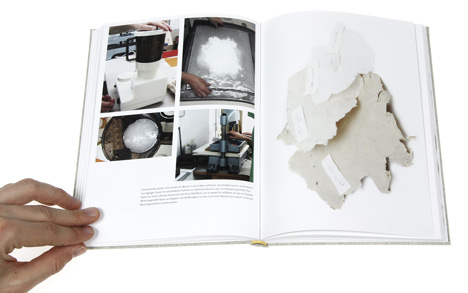
Bacterial-cellulose is a material which is part of a new generations of materials, that are highly specialized, sustainable to produce and biodegradeable. Since the measuring units engineers and biochemist work with become closer, these to professions will overlap more and more in the future. The biochemist will be the engineer of the future. Organisms found in nature will be copied and rebuild for industrial use.
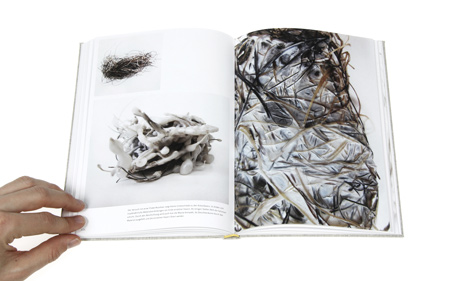
The next step would be the entire new design of artificial systems, that will fulfil the dream of not only imitating nature, but improving it. Regarding all these promising perspective, this still young discipline of science has to be examined critically against the background of possible genetic manipulation of living beings.