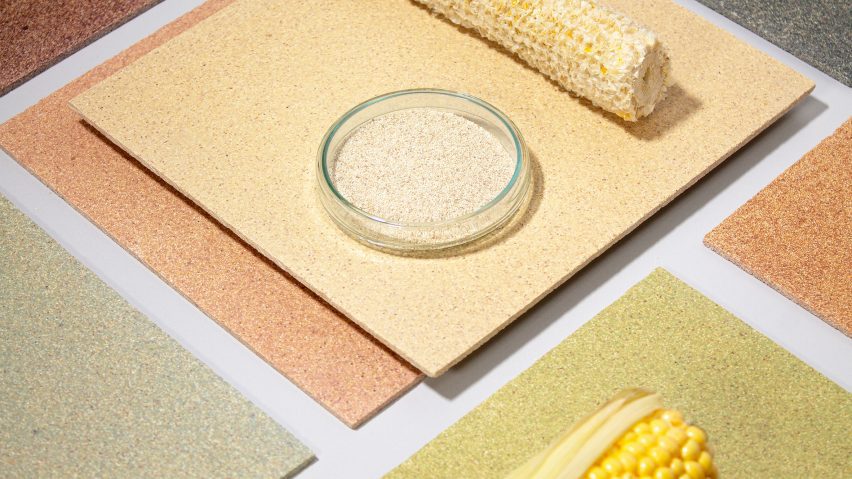
CornWall gives discarded corn cobs new life as tiles
Materials companies Circular Matters and StoneCycling have used corn cobs – one of the world's most plentiful agricultural waste materials – to make interior cladding that is biodegradable and almost entirely bio-based.
Available in the form of tiles and sheets, CornWall is intended as a more sustainable alternative to ceramic interior wall tiles or plastic laminate.
The material is derived from more than 99 per cent renewable, biological sources, is created at low temperatures using mainly solar power and emits less carbon dioxide in its production than was captured by the corn as it grew, the manufacturers claim.
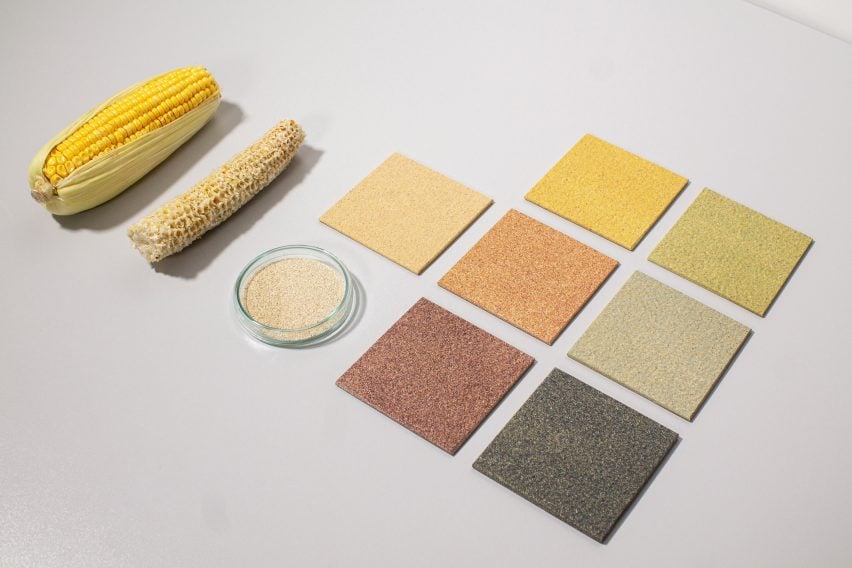
To give the products a long lifespan, Circular Matters and StoneCycling have produced the tiles with a mechanical fixing system, so they can be demounted and reused or given back to the company for cleaning and recycling.
The technology behind CornWall was invented by Circular Matters – a start-up spun out of a lab at Belgium's KU Leuven University, where founder Pieter Dondeyne and his team found a way to process plants to enhance their natural biopolymers and create durable materials.
The team then partnered with Dutch company StoneCycling to channel their technology into a product.
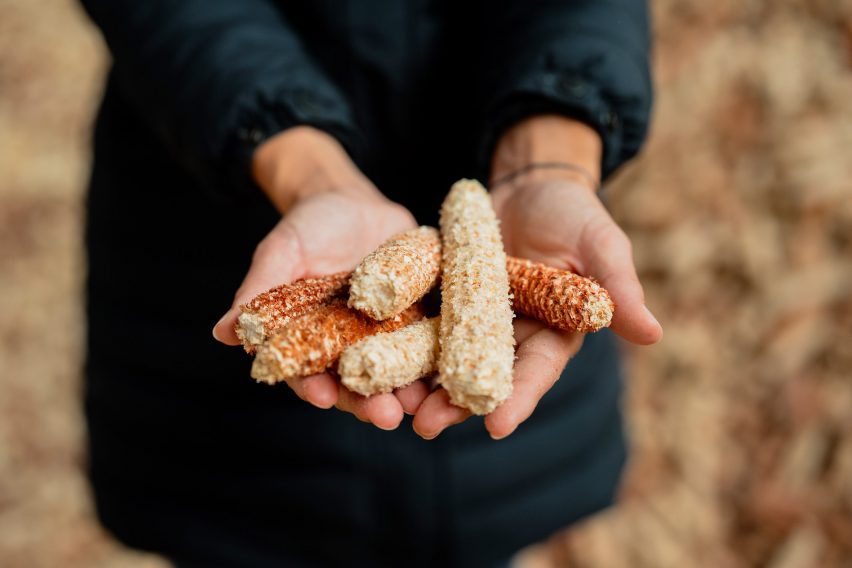
StoneCycling co-founder Ward Massa told Dezeen that the focus on corn came because it is one of the most grown crops on the planet and its waste is abundant.
"What happens when you grow corn for human consumption is when it's ready to harvest, you take off the corn and the corn cob is a leftover material because it doesn't hold any nutritious value," he said.
"Usually, that means that these corn cobs remain on the field and rot away, or they are burned as biomass to generate energy," he continued. "In both cases, you release the carbon that was stored in those fibres – it rots away and it gets released, or you burn it and it gets released."
With CornWall, the carbon is locked away until the tiles reach the end of their life and are left to decompose.
The production process begins with the discarded cobs being collected, dried and shredded into biomass.
This material is then mixed with other agricultural waste, binders and pigments and pressed into a plate material at a relatively low heat of 120 to 150 degrees. As a final step, the tiles are given a thin coating for water resistance.
All of the ingredients are derived from biomass apart from the pigment, which accounts for the 0.5 per cent of the product that is not bio-based – a very low percentage in a field where even products containing small amounts of materials of organic origin are sometimes labelled as bio-based.
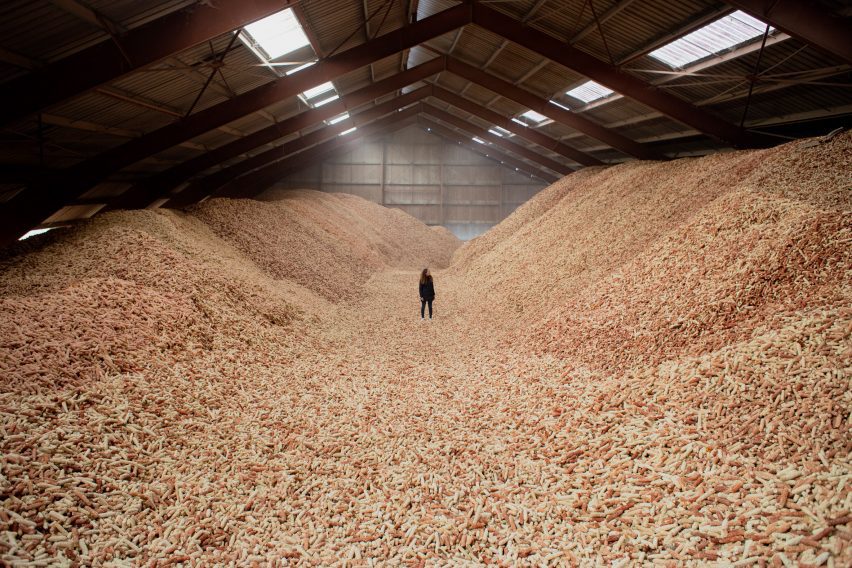
According to Massa, the companies were able to keep the product pure by focusing on interior wall applications only.
"If you want to create a product that can also be used on the exterior or as a flooring or in the shower, then you have to start adding chemicals to bind it, to make it more water resistant and stuff like that," he said.
"We chose to start with this application because it's relatively easy and the binder and the product is nothing else than the natural polymers that are already part of this biomass. Because of adding heat and pressure, these polymers are activated and bind together."
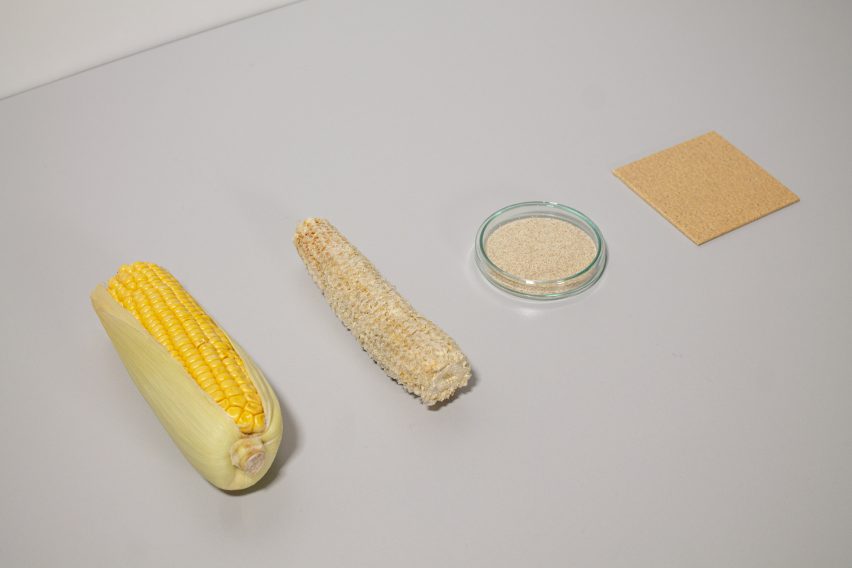
CornWall is also biodegradable according to official standards, with Massa saying it could be buried in a field and disintegrate in a couple of months.
The only thing that would remain is the water-resistant coating, which is not biodegradable but makes up less than 0,001 per cent of the total product meaning it does not affect its biodegradability overall, according to Massa.
"Unfortunately there are no 100 per cent biodegradable coatings on the market yet," he said. "We're working with our suppliers on this but it'll take more time."
Instead, the intent is to keep the product in use for as long as possible.
The companies wants to target retail and hospitality chains that frequently open and close locations – Starbucks is an example Massa gives – and work with them to make sure the tiles stay in a closed loop of material reuse.
He also believes CornWall offers good options for these kinds of businesses in the design stage, as it can be ordered in custom colours and embossed patterns to complement their branding.
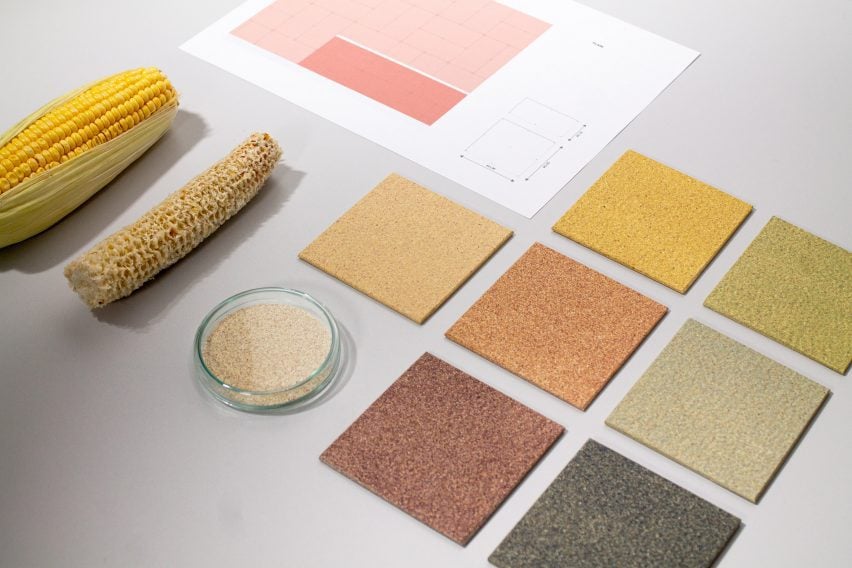
"As far as we are concerned, this will become the new retail material," said Massa. "Especially in those places in retail where they now use materials that are either glued or take a lot more energy to make or create a lot of waste when the shops are being renovated or demolished."
"Production can also be done regionally because you don't need a very complicated factory for it."
CornWall is currently available in a base range of six colours and two sizes, developed in collaboration with Dutch design practice Studio Nina van Bart. Massa says additional textures will soon be added to the line.
CornWall is the fourth product from StoneCycling. The first was the WasteBasedBrick, which is made from 60 per cent waste and was used by Dutch architects Nina Aalbers and Ferry in 't Veld of Architectuur Maken to build their own house in Rotterdam.