Science Studio and Formaldehyde Building for Damien Hirst by Designscape Architects
UK studio Designscape Architect has completed two buildings for artist Damien Hirst. One is an art production studio that appears to change colour from blue to green and the other is a glazed brick building designed for using toxic chemicals (+ slideshow).
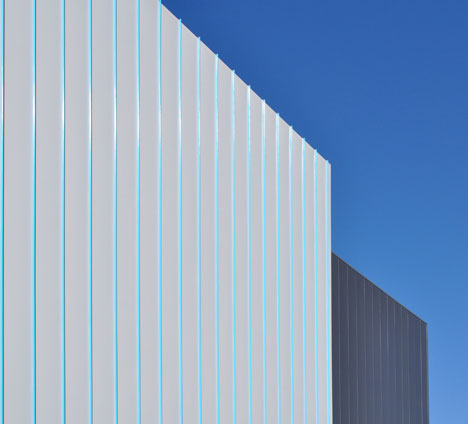
The two buildings are located near Damien Hirst's existing studio in Stroud, Gloucestershire. The Science Studio provides the British artist with a generous workspace, storage facility and private gallery for showing work to clients, while the Formaldehyde Building provides a controlled environment for working with chemicals, particularly the preservative previously used by the artist to create sculptures from dead animals.
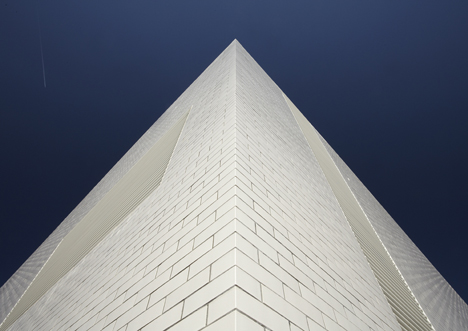
Diffused internal lighting was an important requirement for the Science Studio so Designscape, working alongside MRJ Rundell + Associates, designed a windowless building that brings in daylight through rooftop glazing.
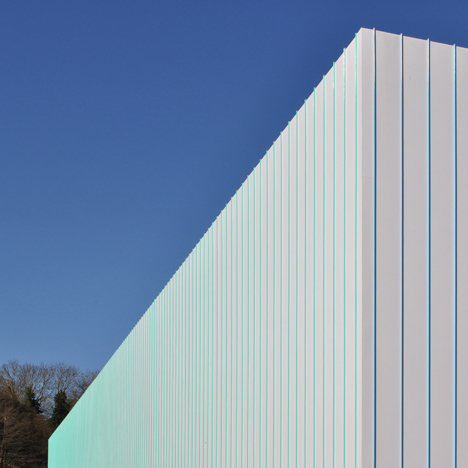
Without windows, the aluminium-clad exterior walls presented a blank canvas, so the architects added stripes of graphic tape to create flashes of blue and green on the edges of each raised seam.
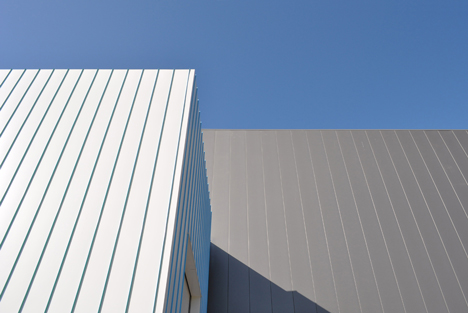
"The aim was to produce a wall that was intriguingly blue from one direction and green from the other," they explained. "If you stand halfway down the elevation, you are not quite sure whether the building is blue or green."
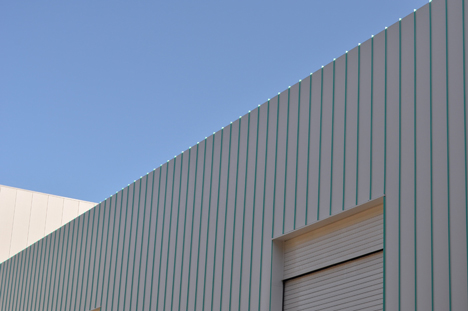
Nine-metre walls give high ceilings to rooms inside the studio, while the gallery is housed in an adjoining 18-metre-high block that is clad with dark grey panels. Interior walls are lined with plywood and plasterboard, providing a strong surface for hanging artwork.
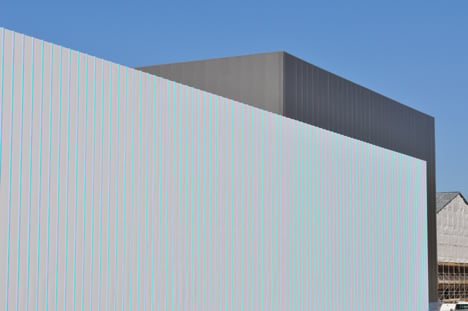
The neighbouring Formaldehyde Building was designed to fit the shape of its site, with one extremely pointy corner.
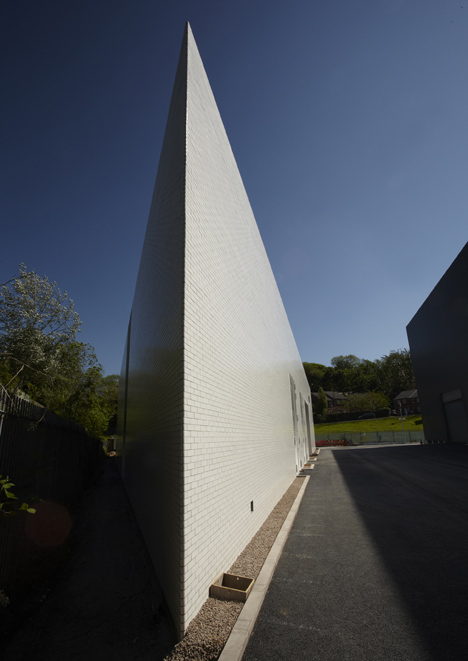
Glazed white brickwork gives a clean surface to the exterior walls, screening an internal layer of concrete blocks.
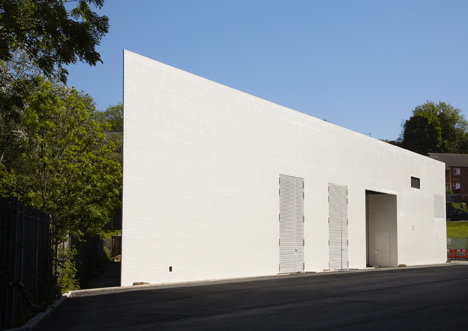
Louvred openings in the walls ensure a constant stream of natural ventilation, creating a safe environment for working with poisonous chemicals.
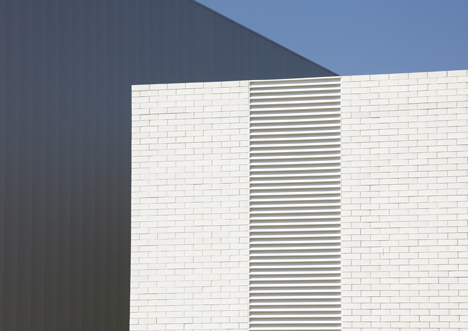
Designscape Architects is a Bath studio led by architects Chris Mackenzie and Spencer Back. Past projects include an extension to an English country house that reverses the building's orientation.
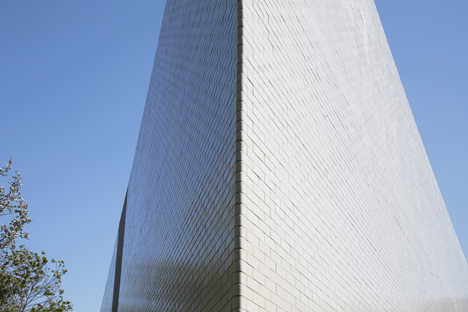
Other studios designed for prolific artists include a galvanised steel workshop for Antony Gormley and a studio for Vivienne Westwood in London. See more art studios on Dezeen »
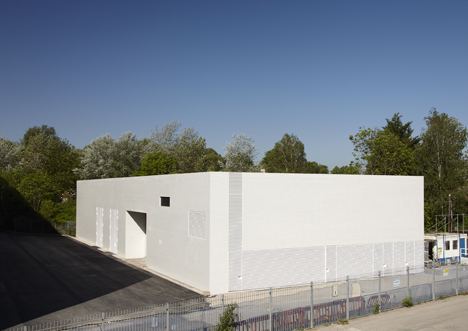
Here's some more detailed information about the construction of each building:
Science Studio
Science Studios is the largest art production studio in the world, incorporating a high security art store and private gallery for showing art to clients.
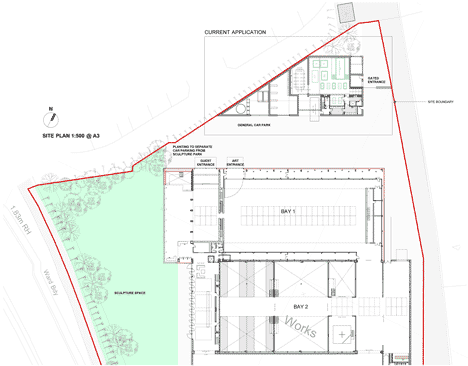
The studios and art stores have stringent requirements for diffused daylight, as well as privacy and security, so all the daylight is provided from the roof except in the staff amenity areas. This results in very big elevations with very few openings - 70 m long and 9 m high without interruption. The walls are clad in 200 mm thick mineral fibre filled composite metal panels which provide an airtight, fireproof, highly insulated and secure external envelope. Inside these walls there is a high density blockwork wall clad in ply and plasterboard to provide a high-strength hanging wall for artwork, as well as providing a services zone, additional security and additional thermal mass.
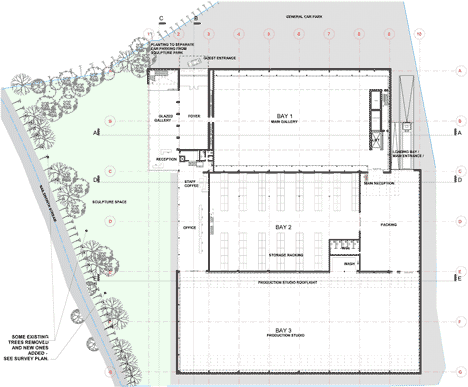
The idea of the standing seams, with blue on one side of the seam and green on the other the Client's brand colours was to make the most of this unusual opportunity with a very big, uninterrupted façade. The aim was to produce a wall which was intriguingly blue from one direction and green from the other. If you stand half way down the elevation, you are not quite sure whether the building is blue or green.
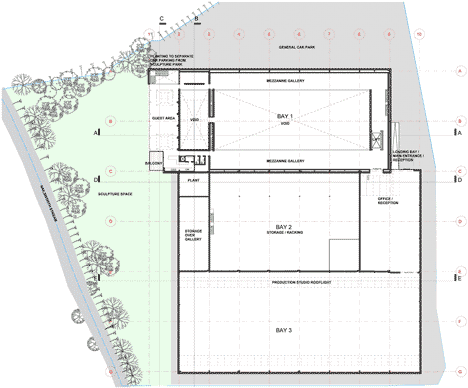
The snap-on overcladding, which protects and extends the life of the mineral fibre panels is made of pre painted hard tempered aluminium. The metal came to site as a coil, and the building was used as a production factory to decoil and form the cladding into trays. Then the colour was applied to the preformed standing seams with a specialist graphic tape (made by 3m).This is a technique very much like a traditional standing seam system, but the seams are preformed and then snap together so no tools are required to close up the seam. This technique is rarely if ever used in the UK, but is more common in the US, but was used in this case because it allowed the application of the coloured tape on the sides of the seams without the risk of damaging the tape during installation.
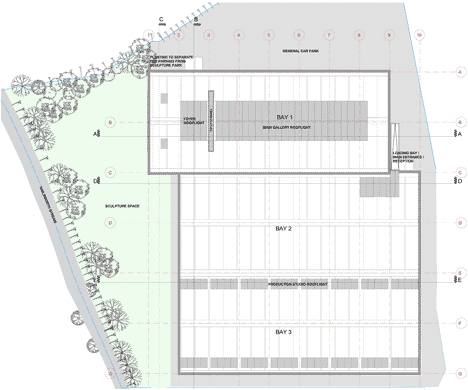
Once formed and coloured, the panels were carried outside manually and hoisted up (they are extremely light and easily handled by 2 people) and then snapped into place on the façade. Setting out and detailing had to be meticulously planned in order to ensure that there were no unfortunate alignment problems at the openings, and the all the details were first trialled on a sample panel which was essential in order to iron out some issues which would otherwise have ruined the simplicity of the façade.
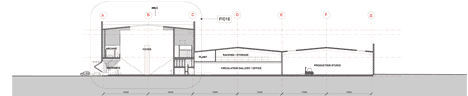
The gallery is 18m high by 70m long, and is expressed as a separate volume and clad in a dark metallic grey Kingspan micro ribbed panel. These panels were made especially long by Kingspan - they exceeded the normal maximum length by several metres, but because they are made in a linear production line, all that was required was to cut them longer than the normal limit, and then arrange special transport to get them to site. The setting out and installation of these again had to be thought through meticulously, so that the cumulative installation tolerances could be accommodated and the cladding module would coincide neatly at the openings without cutting panels. Corners were designed to take out any final tolerances, with the corner panels being mitred along their full length and then fixed using a @damage and fillA technique making a countersunk hole in the cladding using a ball hammer, installing the fixings, and then repairing the panel with an epoxy filler and overspraying the damaged panels. The resulting finished fixing is invisible, but does require exceptional workmanship to get it right. Finally, the mitred corners were covered by a small 100 x 100 mm angle bonded in place and the coping was made to a matching dimension.
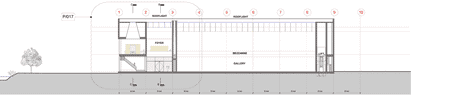
Formaldehyde Building
The building houses a specialist studio facility which uses various chemicals and is therefore fitted out with specialist finishes and services which enable a safe working environment and safe ventilation. The chemicals being used react with and corrode many commonly used building materials, so the choice of glazed brickwork provided a solution that is naturally resistant to the chemicals, but also expresses the use of the building through the choice of external finishes. The client demanded a high quality of finish and detail, and the form of the building - which was dictated by the shape of the site, combined with the other requirements to produce a number of challenges.
The end result is a very high quality and durable building envelope, with all the openings covered in louvre clad doors to produce a fine - grained monolithic, wedge of a singular material.
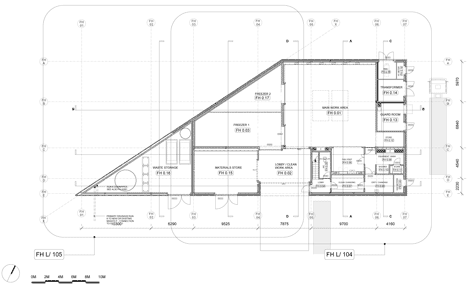
The building is constructed as a steel frame with an internal leaf of concrete blockwork, bracing the frame and providing the inner leaf of a cavity. The brickwork is therefore a ½ brick thick outer leaf of a cavity wall. The choice of glazed brickwork and the requirement for a high quality finish led the designers to decide that a standard 10mm brick joint would not be acceptable, and so a 4mm joint was adopted in order to produce the aesthetic quality the client was looking for. This raised a number of challenges:
» Putting wall ties into a 4 mm joint – The solution was to make every brick as a "pistol", so that the actual brick bed joint was in fact 12 mm, with only the visible face of the brickwork having a 4mm joint for pointing up. This thick bed joint also assisted with the control of thermal movement.
» Avoidance of movement joints in the brickwork – there are only two vertical movement joints in the building façade, and these are disguised by a full height louvred panel. The mortar and the pointing up mix were designed by a specialist engineer and are soft, flexible lime mortar mixes, allowing sufficient movement to avoid thermal expansion cracking.
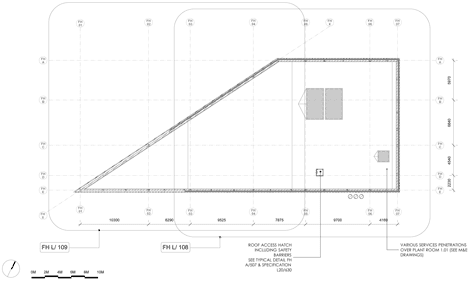
Coordinating brickwork with 4mm joints sizes around openings. As the perpendicular joints are changed from 10 mm to 4 mm it means that, with a whole number of bricks dictating an opening width, then the bricks at the opening jambs will no longer be exactly a ½ brick – one side of the opening will be 6mm more than a ½ brick, and the other will be 6mm less than a ½ brick.
The solutions to the issues outlined above involved the manufacture of a large number of brick specials. The specials used included the pointed end of the building, copings made into precast units, glazed headers for corners and jambs, (not exact ½ brick sizes) slips for cladding lintels, brick slips for cladding a door, and all the "standard" stretcher bricks were cut as pistols. The Design Team worked closely with Ibstock to develop the details and the range and quantity of brick specials.
The nature of this facework is very unforgiving and required unusually tight manufacturing tolerances (dimensions and colour) and meticulously accurate setting out and gauging, using 4mm tile spacers and specially design stainless steel gauging rods to maintain an accurate face dimension of the brickwork in order to achieve the end result.